Lower weight, more comfort and lower unit costs – such are the automotive industry’s requirements for vehicle components. Integrated plastics solutions play a decisive role in meeting these requirements. At the international congress “Plastics in Automotive Engineering”, on April 2-3, 2014 in Mannheim, Germany, ENGEL AUSTRIA will be presenting innovative products and technologies for greater efficiency and competitiveness in automobile production.
Economic processes for composite components
Lightweight design will be one of the focuses of ENGEL’s presentation at the VDI event. ENGEL is a leading partner to the international automotive industry in this market sector. At its own technology centre for lightweight composites, ENGEL co-operates closely with customers and partner enterprises, as well as with universities and research institutes, on developing economic processes for the mass production of innovative composite components.
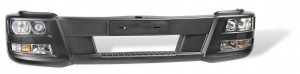
Special attention is given to the processing of semi-finished thermoplastic products (organic sheets and tapes) and to reactive technologies that use thermosetting and thermoplastic systems, such as HP-RTM and in-situ polymerisation. In cooperation with ZF Friedrichshafen, ENGEL recently established an important milestone at the K 2013 with the very first one-shot process for the production of composite brake pedals using the ENGEL organomelt process. ENGEL will be demonstrating its new efficiencies in composite processing at Mannheim as well.
A new level of soft touch
With its Dolphin and Varysoft technologies, ENGEL offers a wide range of extremely economical turnkey solutions for producing premium, soft touch surfaces for vehicle interiors. Compared with other technologies, the new Varysoft process, developed at Georg Kaufmann Formenbau, offers even greater softness while allowing undercuts in the mould design. During a recent “Varysoft Day” in Austria ENGEL presented a highly-integrated and automated production cell that combines a decorative film with thermoplastic carrier and a PUR foam layer in a single step. The highly integrated production cell clearly shows that Varysoft is very close to mass production.
Premium, functional surfaces
ENGEL’s clearmelt technology is also all about premium surfaces. In this case, a thermoplastic carrier is injected and then immediately flooded with transparent polyurethane. PUR makes the surface scratch proof and gives it visual depth. At the same time, functionality can be added to components through smart electronics by inserting capacitive films into the mould. In this way, controls can be integrated into thin decorative trims – both visibly and invisibly. Thanks to this enhancement to the clearmelt process (Multifunctional Surface Technology), the cockpit of the future won’t need any mechanical switches or controls.
LED lenses produced in a record-breaking cycle time
The challenge in the production of LED lenses is to strike the right balance between superior optical quality and high cost effectiveness. And yet ENGEL has achieved this balance through multilayer moulding, a process in which a pre-moulded part is overmoulded with more layers of the same material.
Through improvements to the process, the pre-moulded part is partly cooled outside of the mould, thus reducing the cycle time by half. ENGEL has succeeded in manufacturing 15mm-thick LED lenses in a record-breaking cycle time of 60 seconds.
“Lightweight engineering, surfaces and functional integration will continue to be the most important agents of growth and innovation in the automotive industry,” emphasises Michael Fischer, Head of Sales Technologies at ENGEL AUSTRIA. “Thanks to our capacity for system solutions, we are in a position to develop solutions to these challenges that perfectly meet the technological and business needs of plastics processors.”