ALPHARETTA, Ga., December 6, 2013 – Solvay Specialty Polymers, a leading global supplier of high-performance thermoplastics for the automotive industry, will deliver a technical presentation on the growing use of high-performance polyamides for engine cooling components at the Society of Plastics Engineers (SPE) China 2013 Injection Molding Conference. The event, “Shaping the Future of Injection Molding Through Game-Changing Innovation,” will be held Dec. 11-12 at the Shanghai Marriott City Centre in Shanghai.
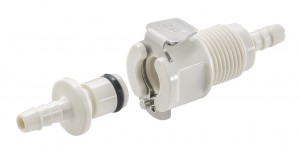
Kirit Desai, technical marketing manager for Solvay Specialty Polymers, will discuss “Integrating Cooling Components by Using Scientific Molding and the Unique Properties of Amodel® PPA.” The demand for engineering thermoplastics continues to climb as OEMs identify new ways to reduce the number and weight of under-the-hood parts to meet tougher CAFE regulations and stricter emissions standards, according to Desai. Over the years, engineering thermoplastics like polyphthalamide (PPA) have replaced metal for thermostat housings and water inlets/outlets.
More recently, the cooling requirements in the car have increased significantly due to several new technologies such as turbochargers, superchargers, exhaust gas recirculation (EGR), dual-clutch transmission (DCT), and start-stop technology, according to Desai. He notes that traditional thermostat housings have become more sophisticated and have evolved into full-fledged thermal management systems in response to more heating and cooling demands.
PPA has filled an important market need, bridging the cost and performance gap between high-volume, moderate-performance engineering resins such as thermoplastic polyesters and nylon, and low-volume, high-cost specialty thermoplastics such as polyetheretherketone (PEEK). Solvay’s Amodel® AS-1933 HS, a 33% glass filled PPA, has been the preferred material in engine cooling components because it retains its high mechanical properties over 5000 hours of continuous exposure to ethylene glycol (engine coolant) at 130°C (266°F).
Another key differentiating factor for Amodel® PPA in engine cooling components is its ability to be injection molded without producing a parting line on the barb of the outlet or inlet tubes. In a typical plastic part, the parting line can be very sharp and cut the tubing during installation, resulting in a coolant leak path. To avoid such a quality issue, OEMs specify no parting line in the barbed area.
Amodel® AS-1933 HS boasts a higher elongation at the recommended mold temperature of 135°C (275°F) compared to other PPAs and polyphenylene sulfide (PPS). The higher elongation allows injection molders to eject the parts from the mold without producing a parting line in the barbed area. In comparison, these complex engine cooling designs are nearly impossible to achieve with standard parting line technology.
Desai will discuss a unique 10-port water outlet for 1.6-L to 2.5-L engines, which is injection molded of Amodel® PPA. The material’s high elongation permits the elimination of the parting line commonly required for injection molding and part extraction to produce this complex part at a cost savings and 450-gram (1-pound) weight reduction versus metal.
Compared to standard polyamides, Amodel® PPA has higher thermal capabilities and is stronger, stiffer, and less sensitive to moisture. It retains its excellent mechanical properties – including fatigue and creep resistance – over a broad temperature range in humid and chemically aggressive environments.