Sinea, a company of the Spanish group IF with a presence in Latin America since 1951, is a multinational manufacturer of plastic packaging with sites in Argentina, Colombia, Chile and Peru, and a strong presence in the manufacturing of caps for soft drinks and polypropylene woven sacks for various industrial applications.
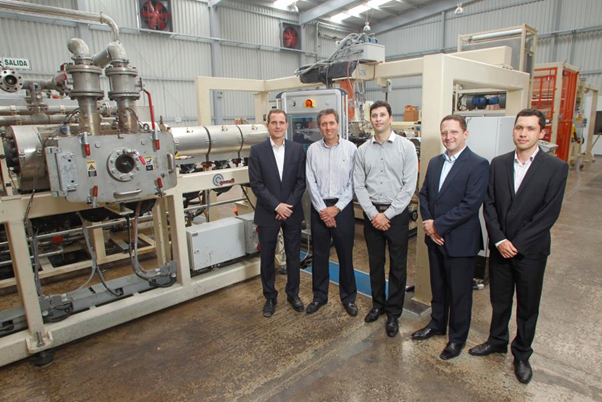
Moreover, in 2008, Sinea entered the recycling sector, handling the entire recycling chain, from the collection of more than14,000 tons of post-consumer bottles annually, to manufacturing flakes, sheet and thermoformed containers.As part of the development in the recycling business, Sinea acquired an additional machine for the production of PET sheet, with MRS extrusion technology from German company Gneuss. Sinea decided to acquire this particular technology because it allows the processing of mixed reclaim material from the washing line directly into a uniform sheet, without restrictions and with an FDA letter of no objection so that the sheet can be used for food packaging.
Sinea and Gneuss already worked together several years ago on retrofitting a Gneuss Filtration System into Sinea’s first sheet line. This project exposed Sinea to Gneuss’ MRS extrusion technology.
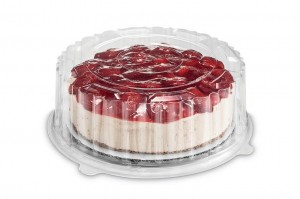
Gneuss’ MRS extruder allows the gentle processing of reclaim and additive materials while offering a very high devolatilization capacity. The polymer melt is delivered into a large single screw drum. The drum contains eight small extruder barrels, parallel to the main screw axis. Installed in these small extruder barrels are the “satellite” screws, which are driven by a ring gear in the main barrel. The satellite screws rotate in the opposite direction to the main screw while they rotate around the screw axis.
This disproportionately increases the surface area exchange of the polymer melt. The extruder barrels, which are cut into the drum of the multi rotation system are approximately 30% open to ensure the optimum melt transfer into the barrels, so that devolatilization can take place without restrictions.
The large and constantly renewed polymer surface enables unmatched devolatilizing performance so that undried and uncrystallized PET bottle flakes can be processed directly, saving not only energy and maintenance costs but also avoiding thermal degradation, which can be common with other sheet extrusion systems. The flakes are gently processed and decontaminated in the MRS extruder, which is utilizing a simple water-ring vacuum system for venting. Thanks to the unmatched devolatilizing efficiency of the MRS it not only efficiently removes all residual moisture, guaranteeing a consistent, ideal IV of the end product, it also decontaminates the polymer so efficiently that the FDA (Food and Drug Administration of the USA) gave it a letter of no objection (LNO) for direct food contact made out of 100% post consumer PET bottle flakes.
After the extruder the melt is filtered with the fully-automatic Gneuss Filtration System RSFgenius without any pressure and/or process disturbances. The RSFgenius represents the latest generation of the Gneuss process- and pressure-constant screen changers. The most important characteristic is the disk, which rotates between two filter blocks. The filter cavities are located in a ring pattern on the filter disk. When the filter disk rotates in small steps (“indexes”), a new, clean filter element is partially introduced into the melt channel. With the constant and large active screen surface area in the melt channel, a pressure-constant process is realized. Just before the contaminated screen is reintroduced into the melt channel, it is cleaned by a patented, integrated back-flush piston. There are no changes to the product caused by screen changes or the back-flushing procedure.
According to Sergio Bravo, VP of Sinea: “With our new MRS extrusion system we can manufacture different sheet formats, which gives us the ability to be more flexible and respond more personalized to our customers’ requirements. One of the best features is the high level of transparency, especially appreciated by customers making thermoformed packaging products for supermarket shelves.”
Internet: www.gneuss.com