As energy demand rises globally, pipeline construction is increasing to secure supplies of oil and gas. These new pipelines are benefitting from decades of experience in pipe protection technology from cathodic current to multi-material coatings and linings. Noru Tsalic of AMI Consulting has studied the markets for materials in steel pipe coating and will give the opening address at the next AMI international conference on Pipeline Coating, which takes place from 24-26 February 2014 in Vienna.
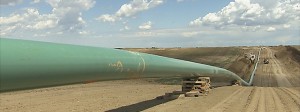
The Petrochina Pipeline Company will also be participating and giving a review of the challenges of long distance pipeline protection in China, while Tial will highlight the use of coatings in oil and gas pipelines in Russia, and Cairn India will outline experience in several projects in that region.
The harsh conditions of the Canadian oil sands have led to new coating developments: International Paint (a division of AkzoNobel) has worked on internal coatings. Quality control is vital to the oil and gas industry and ADCO in the Gulf takes a proactive approach with pipeline coatings. There is field testing of high density polyethylene liners for high pressure water injection pipes by the Kuwait Oil Company and in the United Arab Emirates Anticorrosion Protection Systems is trialling flexible Kevlar reinforced liners for the rehabilitation of subsea pipelines.
The oilfield operator Statoil has undertaken testing programmes of subsea wet insulation materials for deep water applications. There are new demands for pipelines for carbon dioxide capture and storage and the Centro Sviluppo Materiali is assessing the behaviour of coatings in these pipes. The independent test houses like Exova are heavily involved with coating qualification.
There are advances in materials for coatings from top companies like Bredero Shaw, which has a next generation anti-corrosion material for application in 3-layer polyethylene. Borouge has an improved polyolefin topcoat for more demanding conditions like high temperatures and PPG Coatings has a new external epoxy phenolic coating for high temperature, tough environments like sour and alkaline soil. From China the Guangzhou Lushan New Materials Company has an innovative adhesive with high mechanical properties and there are new asphalt-tar coatings from SRC Poisk. Sour gas (hydrogen sulphide) is highly corrosive and Valspar has worked on new coatings to combat this common oilfield hazard.
The factory applied coatings will be rendered ineffective if the field joints are not equally well protected: Canusa has a new factory grade joint coating system for 3 layer polyethylene/polypropylene coated pipelines. Plascoat Systems has worked on 3-layer application technology for joints, bends and fittings. From the equipment side, Inductotherm Heating and Welding has innovative machinery to heat and powder coat pipes simultaneously, which is in use on offshore pipe laying vessels and in multi-diameter pipeline projects. Quality control is a vital concern and Doosan Babcock has studied non-destructive techniques to evaluate field joint coating.
AMI’s conference on Pipeline Coating 2014 in February in Vienna provides a focal point for the pipeline industry to consider advances in long-term performance and improvements in structural integrity.