- Cost-efficient: Injection moulding solutions for high quality and minimum unit costs
- Flexible: Individually designed Allrounders with electric, hybrid or hydraulic drive technology
- Versatile: Medical and packaging technology, multi-component and LSR injection moulding
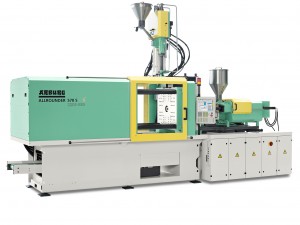
Lossburg. With three exhibits, Arburg is presenting different facets of the overarching topic of “Production efficiency” at the Chinaplas in Guangzou: with energy-efficient electric and hybrid Allrounders, machine configurations for specific products and industries, and automated moulded part production. The presentation also includes special processes such as multi-component and LSR injection moulding. With all these injection moulding solutions, the aim is high cost efficiency – the production of quality products for minimum unit costs.
At Arburg’s exhibition stand no. A41 in Hall 5.1, visitors will be able to see electric, hybrid and hydraulic machine technology. Which of these types of drive is the most economical depends on the requirements of the particular product and sector.
“Packaging” version of the hybrid Allrounder H produces ice-cream tubs in 3.5 seconds
Fast, high-quality volume production using reliable and efficient technology is essential in the packaging industry. And the new packaging version of the high-performance hybrid Hidrive series satisfies these requirements. The Allrounder Hidrive models with the “P” label have been consistently enhanced to produce complete, high-performance solutions, and optimised in virtually all areas. This includes fine tuning the distance between tie bars, clamping force and opening stroke to suit the performance characteristics required by the packaging sector.
Advantages of the Allrounder Hidrive packaging version are fast, precise and energy-saving mould movements thanks to servo-electric toggle-type clamping units, high plasticising capacities thanks to barrier screws and servo-electric dosage drives, and dynamically position-regulated screws, effective injection flow and energy-efficient operation thanks to the hybrid drive concept.
The hybrid Allrounder 520 H packaging model exhibited at the Chinaplas has a clamping force of 1,300 kN and size 400 injection unit. It produces a typical packaging item – an ice-cream tub – in a cycle time of 3.5 seconds.
Electric Allrounder 370 E produces housing component for medical technology
Medical technology is another important sector for the Chinese or Asian market. For this industry, at the Chinaplas an electric Allrounder 370 E will produce a housing for use in a fluid mixing system. The exhibit has a clamping force of 600 kN and works with a size 170 injection unit.The electric Edrive series excels through its precision, reproducibility, energy efficiency and low emissions, and is therefore also suitable for clean room applications. Due to their excellent price/performance ratio, the Allrounder Edrive is an interesting alternative to hydraulic machine technology, and enables economical entry into the world of electric machines.
In this medical application, all parts handling is carried out by a Multilift Select robotic system, which exemplifies Arburg’s robotic range and highlights its advantages. Multilift robotic systems, like the Integralpicker machines, are fully integrated in the Selogica machine control system, and can be programmed easily, reliably and quickly thanks to the teach-in function.
Two-component Allrounder produces orange peeler with LSR element
The orange peeler in question is a true design item, and is produced on a hydraulic two-component Allrounder 520 S with a clamping force of 1,600 kN and size 290 and 100 injection units. With this system, Arburg demonstrates its expertise in both multi-component injection moulding and the processing of liquid silicone (LSR).The LSR component lends a pleasant feel to the handle of the peeler. A local supplier, mould-making firm Hongrita, provides the necessary equipment.
The use of the hydraulic Allrounder S in multi-component and LSR processing is just one of many examples of the amazing flexibility of this machine series, which covers a range of clamping forces from 125 to 5,000 kN. Thanks to the different hydraulic and electric drive alternatives and numerous equipment versions available, Allrounder S machines offer a wealth of configuration options. In this way, the machines can be individually adapted to each injection moulding task, making efficient production a reality.
Production efficiency as our overarching philosophy
The three machines on show at the Chinaplas offer a representative insight into the universal capabilities of the modular Allrounder range. However, this selection also demonstrates how Arburg technology and customer wishes can be perfectly coordinated to suit the individual application. And production efficiency is always at the heart of this. What matters is using resources as efficiently as possible, and exploiting all available potential to the full. The aim is maximum productivity at minimum operating costs, and therefore a high level of efficiency.
To achieve this, Arburg works with the customer to examine the entire value-added chain, and considers all influencing factors, from product design and mould technology right through to production planning. This approach is growing in importance all over the world – which is why it is also a topic at the 2013 Chinaplas in Guangzhou.
Source: www.arburg.com