German automaker Volkswagen (VW) continues to consolidate its part supplier and this is leading increasingly to development partnerships. Apparently, VW would like to adopt, together with its partners, high added value solutions through a one-stop operation. Here, medium-sized companies which, as specialists, offer “very interesting technical solutions” are coming into play. Once such processor is KKT Frölich (Osterode am Harz).
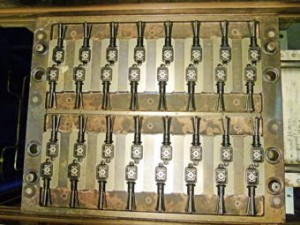
Among the specialties of KKT are shift gates and locking device assemblies used in them. The locking device assembly enables smooth gear changes in manual transmissions. One part employed in this assembly is an elastomeric part developed jointly by VW and KKT that inhibits the transmission of vibrations from the gearbox to the gear knob. The multi-component part was formerly a die-cast component.
In all, the locking device assembly comprises seven individual components. Two of these components are combined in an insert molding process. Base bodies injection-molded from 30% glass fiber reinforced polyamide (PA) are manually inserted into a 2×32 cavity tool mounted in a rubber molding machine and over-molded with nitrile butadiene rubber (NBR) sheaves, each weighing five grams, in a four minute cycle time.
While the operator feeds one set of 32 cavities of the two-station horizontal shuttle mold with sheaths and PA parts, the NBR material is vulcanizing in the vertical elastomer molding machine. “With a cycle time of just four minutes, the operator must act very quickly,” says KKT technical director Klaus D. Wahle, “but we will soon develop an automation solution, so that the process can run independently of the operator – it payser.
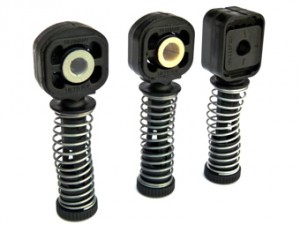
The locking device assembly includes metal springs and other thermoplastic elements. KKT manufactures all elements in this assembly and the entire shifting gate itself, which has a total of 32 parts. KKT delivers assemblies which are ready-to-mount.
Among the latest machinery for this process is the vertical MTF2500/280ergonomic with PC5000touch control from Maplan GmbH (Ternitz, Austria). The Maplan machine, optimized for operation height, is said to be ideal because of its accessibility. “It is very user friendly and also, through the use of the latest technology, very energy efficient”, says Wahle. The energy advantages arise from a “Cool-Drive II” servo-hydraulic system and the temperature control devices in energy-saving DCI design. Mold hal shuttling, meanwhile, is powered electrically.
“On the basis of a 5 working day model, we produce 6-7 million parts per year by using three elastomer machines,” says Wahle, in an indication of machine productivity. “There are different versions of the component which can be delivered as a finished part or assembly part for all vehicles with gearboxes,” he adds. The components find their way into all VW group vehicles including Audi, Seat and Skoda. KKT also plans to establish a joint venture near Denver (CO) that is scheduled to go into operation in 2014.
Source: www.plasticstoday.com/articles/plastic-rubber-combine-critical-gear-shift-component-polyamide-insert-vw-injection-130715a