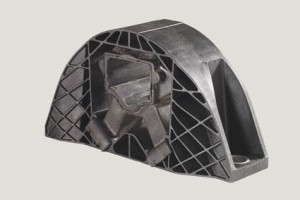
In what could be an emerging trend, plastics are making increasing inroads into an auto application previously the domain of aluminum: engine mounts and supports. Following on from an announcement by BASF (Ludwigshafen, Germany), processor ZF Friedrichshafen AG says it has received a major order for lightweight plastic passenger car engine mounts made from a combination of plastic and rubber. The new plastic engine mount offers a weight advantage of approximately 25 percent compared with rubber-metal designs. The mount is being used in six small and compact car models of Renault-Nissan, as well as in the automaker’s electric cars.
“Lightweight design is one of the key technologies when it comes to reducing the energy consumption of vehicles,” says ZF, “However, automotive manufacturers and suppliers are not able to draw on a superordinate patent solution. In actual fact, the sum of the individual weight reductions in numerous passenger car components represents the key to success,” it notes.
Thus, ZF developed a pioneering rubber-plastic engine mount that immediately convinced Renault-Nissan: It dampens vibrations just as effectively as previous rubber-metal constructions yet weighs approximately 25% less. “Our objective was to increase the maximum lightweight construction potential of standard engine mounts and to further optimize both functionality and reliability,” explains Torsten Bremer, Head of the Rubber & Plastics business unit of the Chassis Technology division.
The ZF engineers mastered this challenge by implementing the engine mount housing using fiberglass reinforced polyamide instead of aluminum continuous casting as was previously the case. A total weight reduction of 25% is achieved thanks to the use of the plastic housing. However, it is crucial that the component remains just as efficient and stable as its predecessor. Furthermore, the part is also said to be “completely insensitive to corrosion and 100% recyclable.”
Thanks to its modular construction, the ZF plastic engine mount can also be designed for various types of engines and vehicles at anytime. “In the automotive industry, we are currently noticing a marked trend towards plastic lightweight construction or downsizing and, as a result, we are also seeing a trend towards increased measures for environmental protection. Moreover, other vehicle manufacturers are intensively testing our innovation for their passenger car models,” says Bremer.
Engine mounts perform important as well as diverse tasks in vehicles: As a joining element between the engine and the vehicle, they prevent undesired vibrations from the unit and driveline being transferred to the rest of the vehicle and, at the same time, they also ensure that noises are insulated. Above all, they must also be strong enough to keep the engine stable within the vehicle, even when traveling on poor roads or in the event of collisions.
In order to develop a polyamide design with these characteristics, the automotive supplier uses its lightweight construction expertise in conjunction with innovative calculation and manufacturing processes: First of all, complex CAD models were created and, based on the latest integrative simulation tools, the ideal solutions are worked out within the context of comprehensive examinations. For this purpose, topological, flow, and strength simulations were performed.
As a result, ZF was in the position to provide close-to-production components without prototype trials and drastically reduce development cycles. This saves both time and money when it comes to development. With the help of the anisotropic simulation, the weight proportion and the alignment of the glass fibers were determined and used as needed. Being able to “read” these simulations requires a high level of “know-how” when it comes to plastic and the understanding of lightweight construction according to ZF.
Source: http://www.plasticstoday.com/articles/plastic-penetrates-engine-mount-application-again-polyamide-20130404