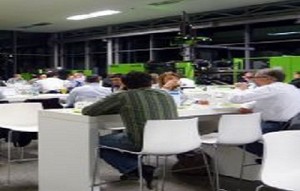
With more than 130 participants, the med.con medical engineering conference organised by ENGEL Deutschland Technologieforum Stuttgart attracted a full house at the end of February. The new ENGEL subsidiary thus achieved its aim of establishing a communication platform for the injection moulding industry in impressive fashion – officially, the organisation does not even open until April.
Experts in medical engineering had travelled to the conference in Wurmberg from across the southwest of Germany and well beyond: Claus Wilde, head of the new subsidiary, and Christian Pum, CSO of ENGEL Holding in Austria, welcomed numerous attendees from the north of the country as well as Italy, Austria and Switzerland. Awaiting the guests was an absorbing blend of expert talks, live demonstrations and networking opportunities as well as insights into the comprehensive range of services on offer at ENGEL’s new site.
“Here in Wurmberg we have the biggest technical centre of any ENGEL subsidiary”, says Claus Wilde. “By changing our exhibits regularly, we can present something new to clients and guests every time they visit. In future, we plan to make many of our product and technological innovations available to customers for trial at a very early stage.”
Cleanliness meets efficiency
At med.con, ENGEL Deutschland Technologieforum Stuttgart presented four medical engineering applications and a total of seven manufacturing cells. The production of pharmaceutical vessels on an ENGEL e-victory 440/120 injection moulding machine using the inject2blow process attracted particularly strong interest. This was the first time the innovation had been seen in Germany: it was only announced by development partners ENGEL and Cantoni last autumn. “Integrating injection moulding and blow moulding processes into a single injection mould means unbeatable efficiency”, underlines Christoph Lhota, head of ENGEL’s Medical business unit.
“Even small batch sizes can be manufactured extremely cost-effectively. We’re getting a lot of enquiries at the moment, especially from the pharmaceutical and healthcare sectors.” The med.con event addressed the trend towards high-performance applications under clean room conditions by producing syringe barrels using an all-electric ENGEL e-motion 940/200 T injection moulding machine. The ENGEL e-motion series has consistently been adapted to the requirements of high performance and high-speed applications. Thanks to new design concepts, particle load and heat emissions do not increase, even under maximum output. The mould room of the ENGEL e-motion machine was conceived as a clean room by ENGEL partner company Max Petek Reinraumtechnik.
Once again, the emphasis was on minimising cycle times in the injection moulding of needle holders using an ENGEL e-motion 310/100 T equipped with high-speed automation by Hekuma and in the production of delicate membranes from liquid silicone on an ENGEL victory 330/120 LIM injection moulding machine.
Warm-up for Medtec Europe
Talks given by experts focused on current requirements, success factors and market opportunities; speakers also offered valuable tips on business practice. Professor Thomas Seul of the University of Applied Sciences Schmalkalden, Hansjörg Keusgen of FOBOHA, Timo Steinebrunner of Braunform, Martin Jungbluth of Max Petek Reinraumtechnik and Christoph Lhota and Professor Georg Steinbichler from ENGEL all addressed the attendees.
By the evening, it was clear to those present that ENGEL – aside from being synonymous with highly efficient system solutions and outstanding medical expertise – is an excellent host too. With Austrian/Swabian fusion cuisine followed by soul and reggae classics courtesy of moojah, ENGEL entertained the guests in fine style. “That was the perfect warm-up for Medtec Europe”, concluded Claus Wilde. The trade fair – in which ENGEL was also taking part – opened the next day in Stuttgart.
Source: http://www.engelglobal.com/engel_web/global/en/22_4500.htm