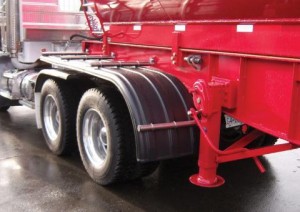
The federally funded National Additive Manufacturing Innovation Institute (NAMII) has awarded funds to its first member projects in applied R&D. The seven projects include several different additive manufacturing (AM) processes and both metal and polymer materials. Founded in August last year, NAMII is the first of 15 planned centers of excellence aimed at revitalizing US manufacturing in the defense, energy, space, and commercial sectors.
As key components in the Obama administration’s billion-dollar National Network for Manufacturing Innovation (NNMI), the institutes are intended to encourage investment in US companies, and make US manufacturers more competitive. NAMII’s formation highlights the fact that 3D printing and AM are now seen as major contributors to US economic health, as does the fact that they were featured in President Obama’s state of the union address last month.
Centered in Youngstown, Ohio, NAMII is paying $4.5 million for about half of the projects’ total costs, while members and their partners are contributing $5 million. Funds were awarded to proposals submitted in response to the institute’s Project Call made last November at the Defense Manufacturing Conference in Orlando, Fla. Proposals had to target at least one of three technical topic areas: materials understanding and performance; qualification and certification; and process capability and characterization/process control. Paramount Industries/3D Systems, Stratasys, and ExOne were listed among the 40 original member companies.
Although none of them were mentioned in the list of winning project descriptions, three of the projects mention technologies specific to Stratasys: fused depositing modeling (FDM) and the high-temperature material ULTEM 9085. Both of these technologies are featured in the winning project, “Maturation of Fused Depositing Modeling (FDM) Component Manufacturing,” which includes small business part producer Rapid Prototype + Manufacturing LLC, the University of Dayton Research Institute, equipment manufacturers, and system integrators. It will look at ULTEM 9085’s properties, with the aim of providing a design guide, data about critical materials and processing, and certification for machines, materials, parts, and processes.
Both technologies are also mentioned in two related winning projects headed by Northrop Grumman Aerospace Systems and Missouri University of Science and Technology: “Sparse-Build Rapid Tooling by Fused Depositing Modeling (FDM) for Composite Manufacturing and Hydroforming” and “Fused Depositing Modeling (FDM) for Complex Composites Tooling.” Other partners include the Robert C. Byrd Institute’s Composite Center of Excellence. Both projects aim at producing tooling quickly and cost-effectively for manufacturing composites. Although ULTEM 9085 is mentioned, its role in both projects is not clear.
Interestingly, Stratasys has already pioneered the idea of using AM technologies for making carbon composites in aerospace applications in its joint work with Oak Ridge National Laboratory. That partnership aims to develop a process based on Stratasys’ FDM for making production volumes of carbon fiber composite components entirely out of autoclave. Its goals are to develop carbon fiber-reinforced feedstocks for FDM, and in-process inspection methods for assuring quality of the parts created.
Another winning project led by Northrop Grumman is “Maturation of High-Temperature Selective Laser Sintering (SLS) Technologies and Infrastructure,” which will focus on developing an SLS process that can manufacture air and space vehicle components from a lower-cost, high-temperature thermoplastic. The project will also explore materials recyclability and reuse.
Along with Arcam’s Electron Beam Melting (EBM) process, EOS’s direct laser sintering (DLS) process is featured in “Rapid Qualification Methods for Powder Bed Direct Metal Additive Manufacturing Processes,” led by Case Western Reserve University. This project will target greater understanding and control of mechanical properties and microstructure in both of these powder bed metal processes, as well as process-based cost modeling for different production volumes.
Another project led by Case Western Reserve University is “Qualification of Additive Manufacturing Processes and Procedures for Repurposing and Rejuvenation of Tooling.” The university will partner with the North American Die Casting Association, die casters, computer modelers, and several additive manufacturers to come up with and qualify methods for repairing and repurposing tools and dies using AM. “Thermal Imaging for Process Monitoring and Control of Additive Manufacturing” led by Penn State University will look at thermal imaging as a method for providing process monitoring and control in two AM processes: electron beam direct manufacturing (EBDM) and laser engineered net shaping (LENS).
The seven projects were the ones among the many proposals submitted that “detailed highly innovative additive manufacturing project ideas, featuring applied research and development, efficient use of digital data, high sustainability, and aggressive education outreach and workforce training plans,” said Ed Morris, NAMII director and NCDMM vice president, in a press release.
More details on the winning projects will be available after project kickoff meetings at NAMII on April 2 and 3. The projects span a range of technologies but appear to be focused on fine-tuning existing AM processes for a variety of different goals. This makes sense for the early stages of what is, in effect, a government-organized industry association. It will be especially interesting to find out what other 3D printing and AM manufacturers are involved, as well as which OEM manufacturers
The next project call will be announced during the RAPID 2013 Conference and Exposition, June 10 to 13 in Pittsburgh, Pa. Any organization can respond to the project call if partnered with a member of NAMII on the proposed project and if that member submits the proposal. NAMII members include industry, universities and community colleges, non-profit organizations, and federal and state agencies.
Source: http://www.designnews.com/author.asp?section_id=1392&itc=dn_analysis_element&doc_id=260918&page_number=1