With Modular Quick-Change™ System from American Kuhne, Barrel and Die Are Taken Off-Line to Tool Room for Cleaning, and Alternate Barrel and Die Are Rolled into Place
YORK, PA, U.S.A., May 27, 2015: A new modular extrusion system enables processors of tubing and other small-diameter medical products to be up and running with a new job just three minutes after the previous run, leaving the tasks involved in die and barrel cleanout to take place outside the clean room environment. American Kuhne will feature a video overview of the system in operation at MD&M East 2015 (Booth 1539).
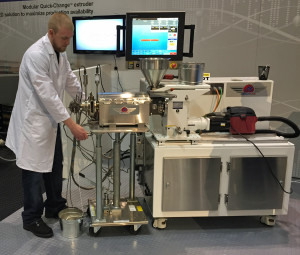
American Kuhne’s Modular Quick-Change™ system has four components: an extruder drive module for the clean room; a purge module for the tool room or other maintenance area; and two barrel modules, one used on-line while the alternate is purged and cleaned. At the end of a job, the “dirty” barrel module, including die head, is rolled away to the tool room for cleanout—a procedure that typically takes two hours. The alternate barrel module, preheated and with the new job recipe pre-loaded, can be installed on-line in about three minutes.
Based on Single-Minute Exchange of Die (SMED) concepts, the new system is especially suited for medical and other contamination-sensitive applications, according to Bill Kramer, chief technology officer for extrusion systems. “The medical industry demands best practices in machine design that provide stability, efficiency, and control,” said Mr. Kramer. “Beyond these, this SMED solution enables a novel hot-swap process that reduces to minutes what would otherwise take hours and, perhaps more importantly, preserves the clean room environment.”
The Modular Quick-Change system is available for extruders up to 2 inches (51 mm), though custom-engineered systems are available for larger units.
How Production Downtime for Job Changeovers Is Reduced
● Switching jobs. This roughly three-minute process takes place as follows: After dumping unused material from the hopper and vacuuming material from the feed throat, the operator unbolts the dirty barrel module from the drive module, unplugs its electrical connections, rolls it to the tool room for cleaning, and rolls a clean, preheated barrel module to the clean room, where it is positioned for mounting to the drive module. After inserting a feed section liner into the drive module, the operator bolts the barrel module to the drive module, plugs in the electricals, adds material, and starts the new run.
● Purging and cleanout. After inserting a feed section liner into the purge module, the operator puts the purge module into “engage” mode to align the screw keyways, mounts the dirty barrel module to the purge module, turns off engage mode, bolts the barrel module to the purge module, and plugs in the electricals. The operator then unbolts the die head clamp for cleanout, runs out the material remaining in the barrel, and uses a pneumatic screw pusher to remove and clean the screw. After replacing the cleaned screw, breaker plate, and die head, the operator pre-loads the recipe for the next run and preheats the barrel module to have it ready for use.
Website: www.grahamengineering.com