IML Competence in the Reference Class: “Make It Simple, fast, and Proven“
The IML Competence collaboration of IML experts involving Beck Automation AG, Ernst H. Furrer AG, Glaroform AG, Viappiani Printing and BFA Solutions Ltd.demonstrates the possibilities of a high-performance system for IML technology (In-Mold Labeling) at K 2013. Visitors benefit from the full expertise that this collaboration brings to the table, from the injection mold and automation to labeling through to the final product.
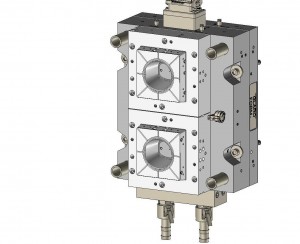
IML Competence stands for the high quality and exacting standards we have come to expect. K 2013 will see new impulses on simplified operation, QA measures, and documentation options for IML in food and non-food applications. The presentation showcases the entire IML range as a reference manufacturing cell.
The long-standing IML Competence partnership permits high availability and top class performance for manufacturers while being easy to operate and offers new QA measures and documentation on how to improve the added value of new systems.
IML Technology to Order: Every Component Counts
As IML is a highly dynamic process, profitability is derived from the level of system components. Electrostatic charging and core alignment are the key processing points in the procedure. First the labels are sucked from the label magazine. In the second, the labels are placed on the cores and held with vacuum. The automation cores move into the cavities to transfer the labels. In this stage the labels are blown against the vacuum, electrostatically charged and thus placed and held in the cavities so they are form-fitting. This makes the level of process design and quality of the label key factors in process safety, reproducibility, product quality and economic efficiency.
Swiss-Made” Mold Technology for Thin-Wall Technology
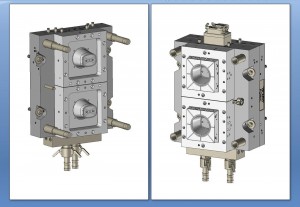
Glaroform AG in Näfels, Switzerland, shows a fast running injection mold with 2 cavities for a round-oval 500 ml food container. The mold has an on-site hot runner system with pneumatically operated needle valves. The molded part is decorated with IML on the sides. The mold is equipped with a form-fitting and highly efficient cooling system, in order to guarantee a very fast cycle time with reproducible product quality. Formfitting cooling also effectively reduces warping of the part.
The mold satisfies the latest standards in design engineering, and is made from pure quality too l steel. To ensure the long period of application for molds for which Glaroform is renowned, the mold is manufactured using the latest surface coating processes for excellent process safety,and with the utmost precision in tight tolerances. The thin-walled product has an average wall-thickness of 0.4 mm and a weight per unit of approx. 11 g.
Highly Effective and Easy To Use: Automation with QA Module
Beck Automation AG in Oberengstringen, Switzerland, adds a highly dynamic automated IML system to the manufacturing cell. The modular cell raises the bar in speed, availability and process reliability in IML automation. The application cycle time is less than 3.0 seconds. Beck’s system is equipped with the latest in control and drive technology. It is operated by touch screen. An integrated remote access provides the option to log into the system from outside in order to provide cost-efficient and fast customer assistance when required. With this approach, Beck Automation has taken its systems’ user-friendliness to a new level.
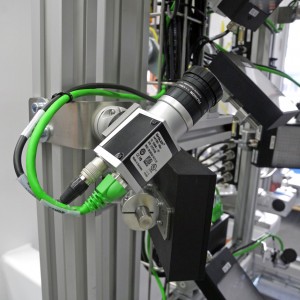
A camera inspection system from Omron is used for quality control of the manufactured containers. Any parts determined to be flawed are rejected by the Q-SORT LINE after inspection, and collected in a NOK parts box. The good products are then stacked and removed from the system via a conveyor belt. The Q-SORT LINE can be retrofitted: Existing plants can be upgraded with this QA module. This separation of OK/NOK units in a highly dynamic system provides a manufacturer with a completely new level of assistance to ensure that quality assurance standards are satisfied.
Energy-Efficient Cooling Concepts
The renowned company Ernst H. Furrer AG in Dällikon, Switzerland, supports the application with temperate cooling water using the newest cooler technology. Socalled “free cooling” can be deployed optionally. This means that cooling is achieved with cold outside air, as long as the difference is sufficient to permit the desired medium temperature. The use of compressors is unnecessary in this phase, enabling power cost savings of up to 60%.
Accentuate Product Communication with High-Quality Labels
Viappiani Printing in Segrate, Italy, produces labels for this exhibit based on a 60µ EUP orange peel film made by Treofan. The container’s round-oval shape requires labels to be stamped with the utmost precision and that can guarantee the fast cycle time with a good electrostatic charge. The sheet offset method guarantees the best print quality for both the 4-color photographs and the Pantone colors. Viappiani can print IML labels with up to 8 colors including lacquer coating. This gives users a broad range of options to lend their products an upmarket look and feel and accentuate them at the point of sale.
Spotlight Shines on Complete Documentation in IML
BFA Solutions Ltd. for the first time ever presents the production data capture for a closed cell (MDE) in packaging for IML Competence. The product information system PiSolutions jointly captures, displays and chronologically logs the process data, data sets, orders, error messages and status information of the exhibited application. This is a forward-looking step toward Industry 4.0 and complete data recording of a variety of components with different controllers.
In the case of the exhibited application, the injection molding machine data is recorded by the machine’s standardized Euromap63 interface and combined with the automation data received from an OPC interface. This data is then stored and visualized in a central database. This is made possible by the newly created combination of the bundled solutions Pi_Inject and Pi_Assembly, each of which include the industry-specific features of MES PiSolutions, thereby ensuring a swift and smooth transition from injection molding and automation. This type of data capturing supersedes the installation of several independent BDE/MDE systems within a production environment and can be used as a single, central module which can be linked to a master ERP system.