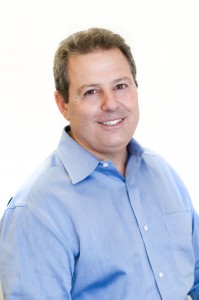
The late 1980s and 1990s represented a major transition period for medical plastics. Major resin producers were scared off by litigation issues following failures of silicone implants. At the same time, markets such as catheters were just emerging and needed development partners.A new generation of entrepreneurs emerged to fill the gap.
One was Larry Acquarulo, who left compounder LNP ito start a specialty medical compounding business called Foster Corp. (Putnam, CT) in 1989. It was “hand-to-mouth for a few years” Acquarulo told Plastics Today in an interview at MD&M West in Anaheim, CA. Now sales are in excess of $25 million. The company operates more than 10 twin screw extruders with outputs ranging from 10 lbs/hour to 1000 lbs/hour in facilities in Putnam, CT and Las Vegas, NV.
The company is making innovations in nano compounds, bioresorbable plastics, combination products and other areas in a Polymer Innovation Lab with a twin screw extruder, injection molding machine, and film/tube extrusion equipment. Starting below, Acquarulo discusses what’s happening in the medical plastics business in a two-part interview with Plastics Today.
Q. Larry, how does Foster fit in?
Foster was founded on providing highly specialized polymer compounding services to the medical device industry. At the time, medical devices such as catheters were in an emerging phase and the volumes consumed were relatively small. Many traditional compounders were not set up to service these volumes.
Today, a great deal of innovation is occurring in implantable devices and the demand for suitable polymers is evolving and expanding. Due to regulatory requirements, small volume consumption, and high profile litigations in the 1990s related to implants, many material suppliers are hesitant to serve this market. Those that do often charge a premium associated with higher regulatory compliance costs, risk management costs, and lower volumes purchased.
Foster has embraced serving emerging implant customers with customized polymer solutions as we did with catheter customers in the 1980’s. However, not all raw material suppliers are willing to serve this market. Sourcing raw materials can sometimes be a challenge for permanent implants.
What is the projected growth rate this year for medical plastic compounds in the USA? Is Foster growing? Adding equipment this year?
Medical plastic compounds are used in a wide variety of segments within the market, such as devices, equipment housings and tray and fabrics. A substantial amount of our compounds are used in devices, which continues to grow at approximately 5-10% on average. We anticipate plastic compounds used in devices will grow within this range. To serve larger volume medical applications outside of devices, such as custom colored polymers for wound care and disposables, we recently invested in a large twin screw extruder capable of over 1,000 lbs/hour throughput.
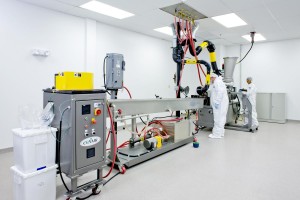
It seems that device makers are anxious to develop differentiated products and want suppliers to contribute ideas. Do you see that trend? How can comppoudners contribute? (Physical, electrical effects? Something else?)
There is definitely a trend towards devices with unique attributes from their materials of composition. Combination products, with drugs blended into polymers, for local drug delivery or controlled release is one of the most exciting. In our GMP cleanroom we are able to blend certain drugs into compatible polymers to produce compounds with active pharmaceutical characteristics.
We have also been doing considerable work in the area of antimicrobial compounds used for devices in which bacteria buildup and infection is problematic.
Another area involves nano-reinforcements used to enhance the physical properties of plastics at the molecular level. This is important for vascular catheters that are getting smaller with thinner walls, but must be stiff enough to be pushed through vascular pathways. Standard fiber reinforcements are simply too large to be used in these extremely thin walls.
Some design engineers have complained that companies have launched new medical grades, forbidding use of other grades for medical applications, even though other standard or FDA grades had been used for medical applications for a long time. How valid are the complaints?
Regulatory requirements for medical devices have been gradually moving up stream over the past several years. Tighter material specifications for medical applications, USP and ISO-10993 testing compliance, no-change policies for manufacturing or formulations are some examples. In many cases these requests have been made of the raw polymer suppliers. This has made polymer suppliers more aware of the unique requirements of the medical market.
At the same time, the medical market often commands a lower volume of raw materials than other markets, such as automotive or industrial. These converging dynamics have resulted in some companies stepping forward to service the market with specialized grades for medical applications, while others have exited due to perceived risks or returns.
Source: http://www.plasticstoday.com/articles/foster-ceo-discusses-emerging-trends-medical-plastics0403201301