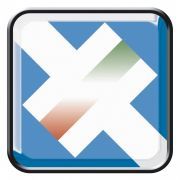
ENGEL will be focusing on precision combined with outstanding economic efficiency at Eurostampi 2013, which takes place from 21st to 23rd March as part of the industrial fair MECSPE in Parma/Italy. An ENGEL e-mac 310/100 will be producing spacer rings for sanitary facilities and once again demonstrating the performance levels of ENGEL’s new all-electric injection moulding machine series by doing so.
The ENGEL e-mac has set new standards in the manufacture of technical parts. From injecting and metering to mould and ejector movements, all drives in the ENGEL e-mac are servo-electric. This guarantees the best possible precision and process stability while maximising the effectiveness of the machine as a whole. The drives are operated by a modern axis system solution involving a stabilised intermediate circuit. The braking energy is recovered and fed back into the grid, which results in a very high level of energy efficiency. The synchronous movements of the drive axes ensure fast cycle times.
With an acceleration of over 20 m/s², the injection axis of the ENGEL e-mac is now the world’s fastest of its kind.This means that during the three days of the trade show it will be able to make the spacer rings from a highly crystalline polyamide in a quadruple mould by Persichetti (Fratta Todina, Italy) with a cycle time of just seven seconds. The cycle time taken by the ENGEL e-mac to carry out this task is 20% shorter than that required by a hydraulic injection moulding machine. The machine’s high precision levels also ensure that the quality of its products is always high and therefore increase productivity as well.
High output from a small footprint
Higher energy efficiency levels, fewer rejects, and shorter cycle times – it’s not just when it’s producing precision parts that an all-electric injection moulding machine can have advantages. The ENGEL e-mac also offers customers the opportunity to save in another way, because it is so compact and takes up very little space. In addition, its tried-and-tested CC 200 control unit, which guarantees full modularity and automation technology integration, provides flexibility. The new series has four machine sizes with clamping forces of 50, 75, 100, and 180 tonnes.
ENGEL will be teaming up with partners at Eurostampi. In cooperation with Moretto (material management), Frigel (refrigeration technology), Leonardi (plastics), and Persichetti (mould construction), ENGEL will be covering the entire value chain for technical part injection moulding at a joint stand.
Source: http://www.engelglobal.com/engel_web/global/en/22_4430.htm