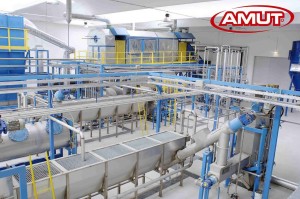
AMUT is pleased to have been selected as an integral part of the new project of Carbon LITE Recycling LLC (an HCP company): a 20.000 m² plant will process post-consumer bottles into pcr PET pellets that can be used to make new bottles. The output is approximately of 45.000 tons/year of finished product.Total investment in equipment and infrastructure will exceed $60 million.
CarbonLITE is one of the world’s largest company specialized in bottle-to-bottle recycling, producing pcr PET bottles and serving the major beverage brands. Acquiring the AMUT plant, Carbon LITE doubles its capacity setting it in the new plastic recycling facility in Abilene, Texas. Another plant is already operating in Riverside, California. Abilene plant will be supplying Nestlé’s bottling facilities near Dallas.
AMUT has been chosen not only for the unquestionable experience in manufacturing washing plants at high capacity and for the proven quality to bottle-to-bottle process guarantee, but also for the innovative pre-washing and dry cleaning systems suitable to deal even with tough materials.
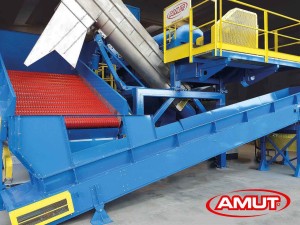
AMUT machinery and technology will be utilized in many steps of critical areas for cleaning the PET bottle stream. Starting with the De-labeler (DLB-60 model – patent-pending ) full-body shrink sleeve label-removal system, additionally the patented AMUT PW-180/5 High Friction whole bottle wash technology will be incorporated for cleaning the whole bottles prior to the AMUT wet grinding process. For the final cleaning of the PET flakes AMUT will be supplying their patented hot Flake Friction Washing technology AX 150/5 machinery.
The De-Labeler (launched with great success into the market in 2013) is able to remove full-body shrink sleeve labels, other labels and general dirty using a complete dry pre-washing system (water free).The shrink labels represent up to 15% of the capacity of bottles in USA. The De-labeler is the best solution to solve the problem and not losing material.
For the food-grade purification and pelletizing will use the prime technology from EREMA North America Inc. The new plant’s front-end, bale-opening and bottle-sorting will be built by Bulk Handling Systems of Eugene, OR using sorting modules from its subsidiary, NRT of Nashville, TN.