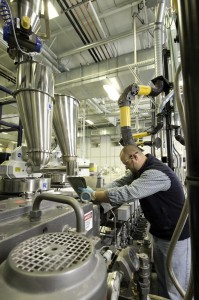
Decreasing catheter size, bioresorbables and the increasing specialization of medical care are triggering changes in the plastics compounding business. Foster Corp. CEO Larry Foster discusses these and other trends in the conclusion of an interview with Plastics Today that began yesterday.
Q. Larry, what do you see as the biggest trends in medical compounding?
On one end of the spectrum, compounding is moving towards smaller, more specialized applications in which both the polymers and additives are extremely expensive. This includes combination products and hot melt extrusion for pharmaceutical drug delivery.
On the other end are the larger volume applications, such as wound care and disposables, in which the markets continue to grow but healthcare cost pressures and competition demand more price improvements from raw materials. For compounders, throughput is one way to achieve this, yet quality cannot be compromised in the process.
What’s the future for bioresorbable compounds and what is Foster doing in that area?
Bioresorbable compounding is a fast growing area for us. We do a great deal of work in blending specialty additives into bioresorbables to give them unique properties. The two most common include bone-growth additives for orthopedic devices and active pharmaceutical ingredients for local or controlled release drug delivery.
What’s the potential for nano reinforcement in medical? Does Foster have any applications? What types of compounding equipment modifications are necessary?
We have been working on nano reinforced polymer formulations for more than a decade. While the equipment to manufacture such formulations is commonly used in other medical device compounding operations, the process is highly specific and proprietary. Without the right process, these fine particles can agglomerate in the polymer. Dispersion is critical. We have experienced considerable interest today as catheters and similar devices continue to decrease in size and wall thickness while still demanding property performance.
Demands for cleaner (purer) medical compounds are growing. What steps can be taken by a medical compounder to reduce extractables?
One of the most noticeable demands from device companies has been for our melt filtration services to remove gels and contaminants in polymers. While these go unnoticed in many large applications, they make all the difference in thin wall tubing and balloons.
Are delivery forms for medical compounds changing (pellets, tubing, film, etc.)?
Pellets are still the dominant delivery form for medical compounds. However, in applications that require highly specialized compounding in a GMP clean room environment, such as implants or drug delivery applications, companies will often request that we provide the material in a more finished form to avoid additional operations outside of the clean environment. These forms have included film, fiber, rod and tubes.
Do you see a trend toward or away from certain types of plastics?
Consumer and regulatory concerns regarding phthalate plasticizers in PVC and Bisphenol A (BPA) in polycarbonate have certainly impacted the use of these materials in certain medical devices.
Is the role for a custom compounder specializing in medical becoming more or less important given new resin producer interest in the market and increasing complexity of requirements?
Our role has become more important than ever, as the bridge between the device companies and the raw material suppliers. Device companies are seeking long term supply stability of materials suitable for their applications. Once the device has FDA or EU approval, changes become considerably more difficult. At the same time, material suppliers want to ensure their materials are suitable for application uses. Often, we are asked to ensure the needs of both parties are met.
How well is the effect of additives (pigments, radiopaque fillers etc.) on mechanical properties understood by medical device design engineers?
Experienced engineers who have worked with radiopaque filled materials, or custom colors, understand the relative impact these additives have on the inherent physical properties of the polymers. However, this is largely empirical. Foster is making a concerted effort to test and publish data for custom compounds using these additives at different loading levels.
How can Foster meet global needs of its customers? Do you need Asian and European outposts?
We have been serving global customers for years with highly specialized materials and volumes that can be shipped overseas with minimal impact on the overall value of the compound. That said, development of our polymer compounds requires understanding customer applications and tailoring properties to meet precise requirements. We achieve this with regional technical and commercial support.
In North America we have direct Foster staff located in East, Central and Western regions. We recently relocated one of our engineers to India to serve this emerging medical region in Asia, including India, China and Korea. Our representative in Europe, MedNet, is headquartered in Germany covers the entire region with field staff in Germany, France, Israel and the United Kingdom.
Source: http://www.plasticstoday.com/articles/bioresorbables-miniaturization-top-trends-medical-compounding0404201301