At K 2013, Bayer MaterialScience will present a complete material concept for the future design of automobile interiors, which also takes into consideration the cost-effectiveness of the manufacturing processes.
“Drivers are placing increasing value on customized and personalized interior appointments,” says Eckhard Wenz, an expert for automotive applications at Bayer MaterialScience’s Polycarbonate Business Unit. This includes pleasant, atmospheric lighting, a seamless design and transparent, colored and diversely decorated surfaces. “Other trends include natural materials, expanded functionality and infotainment – and with perfect workmanship and the greatest possible impression of quality.”
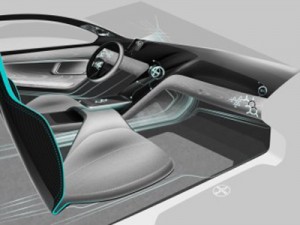
One example is innovative display with a homogenous, 3D surface, but sharp images and high brightness. This is made possible by rear projection technology, in which a light source behind the film transforms it into an illuminated display. Bayer has developed a special polycarbonate film, Makrofol RP (RP stands for Rear Projection) for this application.
“This technology opens up a whole new type of information to drivers, with only selected information being displayed,” explains Dirk Pophusen, Head of Film Applications in the Automobile in Europe.
When switched off, only an elegant, matte black surface is visible. The driver is not distracted by underlying structures or other effects.
Slim, retractable components that are only visible when switched on are made with blends from the Bayblend line and the transparent PC Makrolon LED. The latter was specifically developed for lighting engineering applications.
Besides Makrolon LED2245 as the material for the light guide, refined Bayblend grades are used as the carrier material. The carrier materials are flooded directly in the mold with polyurethane (PU) coatings, such as Desmodur and Desmophen. High quality reproduction of the mold surfaces enables structured, grained, high-gloss and matte surfaces to be produced simultaneously.
Fabrication using the DirectCoating method co-developed by Bayer is cost-efficient and can be completed in a single step. This method combines injection molding and reaction injection molding (RIM). Among the companies with which Bayer MaterialScience is collaborating in this field is KraussMaffei Technologies GmbH, which markets the method under the ColorForm name. The machinery manufacturer will be demonstrating the production of a component under near-series conditions at its stand.
“With this technology, robust, three-dimensional components with a customized appearance and haptic can be cost-effectively produced in just one manufacturing step,” remarks Mr. Wenz.
K 2013 will be held from October 16-23 in Düsseldorf, Germany.
Source: www.adsalecprj.com/Publicity/MarketNews/lang-eng/article-67007390/Article.aspx