Automatik Plastic Machinery has developed a new elastomer feed roller specially designed to meet high demands in terms of abrasion and thermal loading.
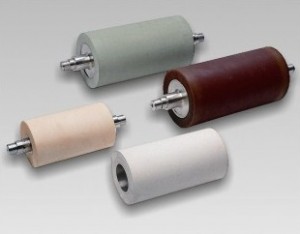
This new roller, EL 24, features a high thermal load capacity of up to 170°C, which is well above that of conventional rollers in use, the company says. It also offers better frictional resistance and compression behavior. The new roller is white and more importantly for the semiconductor industry, is also silicon-free.
Feed rollers are exposed to a wide range of loading based on the different materials processed in compounding and masterbatches. The products they process are soft, brittle, abrasive and/or very hot. The feed roller therefore has to be closely adapted to the material being processed. Demands on elastomer rollers are very high particularly in relation to abrasive materials incorporating reinforcers such as fiber-glass or high-temperature additives.
In addition to external influences, feed rollers are also subject to continuous deformation due to the rolling motion as well as to compression by the inflowing strands. The factors of hardness, abrasion, elasticity or compression are key in determining whether a coating bounces, damps, shrinks or sets quickly. Ever more specialized materials are leading to a steady rise in demand for feed rollers adapted to the materials being processed.
Automatik notes that the new EL feed roller is designed specially to handle high loads, and customers imposing very high demands and subject to very high loading on feed rollers have reported that using the EL 24 results in four to five times longer life.The company also offers a backup package for the rollers enabling them to be exchanged for recoating within a few days.
Source: http://www.adsalecprj.com/Publicity/MarketNews/lang-eng/article-67005366/Article.aspx