Introduction
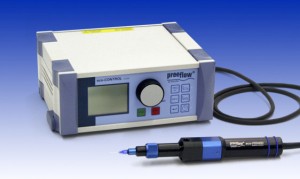
An ideal process involving the application of fluids and liquids like adhesives (including thermally or electrically conductive), oil, ink, paint, grease, solder paste, enzymes or catalysts would be to have a predetermined volume of material applied to a location with accuracy and consistency. This may have more importance in fields like medical device manufacturing (validated repeatability) or microelectronics (precision), but all engineers want to remove variability in their process.
Time/pressure Dispensing
For over 30 years, the dispensing of industrial fluids has been improved by simple time/pressure dispensing machines (also called dispensing controllers). A syringe-like barrel with the liquid inside is attached to the dispensing controller, which upon demand, pushes compressed air into the larger end. This compressed air can be a timed pulse. The air pushes the liquid out of the smaller end of the syringe barrel, usually though a dispensing needle or nozzle. The amount dispensed is dependent on 1) the rheology of the liquid (viscosity, thixotropy, etc.), 2) the air pressure, 3) the time of the pulse of air and 4) the size of the orifice in the needle.
The latter three factors are selectable, and with the choice of a suitable combination of these, most flowable liquids can be dispensed in beads or drops with a reasonable amount of accuracy and repeatability. Many thousands of these machines have been sold, with major benefits to users, including material control and health & safety. Typically, these devices are used manually or in a semi-automated process. With low viscosity liquids, and the finest needle size (ID of about 0.25mm), quite small dots can be dispensed.
Limitations of this approach include having to have the liquid packed in a dispensing syringe barrel; many materials are available from manufacturers packaged appropriately, or they can be filled subsequently by a third party service or in-house. Any air inclusion in the barrel will affect deposit accuracy, so the filling process (which may include centrifuging) is a factor. One variable which is difficult to control is material viscosity; the less viscous the fluid is, the greater its’ ease of movement, and the larger the dispensed amount will be for the same settings. Viscosity can change with ambient temperature, or with repeated quick air pulses.
The material may also change due to curing e.g. a mixed epoxy adhesive. Another issue is the variability in dispensed quantity as the syringe barrel empties. The amount of compressible air in the system increases accordingly, which means that the same pulse of compressed air from the dispensing controller has a lesser, delayed impact on the liquid, resulting in smaller deposits.
Dispensing Valves
Some of the limitations of simple time/pressure dispensing can be mitigated by the use of dispensing valves. These are typically pneumatically controlled valves into which the material is fed (usually under pressure from a reservoir) and which allow the material flow to be started/stopped or otherwise controlled. A previous article gives more detail.1 A fully automated fluid application operation often uses a dispensing valve, as it precludes the need for the exchange of empty barrels for filled ones, for example.
Positive Displacement
The quest for a true, volumetric dispense has led to the development of valves which work on a “positive displacement” principle. Within the valve, a cavity of the desired volume is filled with the liquid, and then this volume is ejected – mechanically or pneumatically. For example, this can be achieved with a tube which is pinched by pistons at either end to form a cylinder of the appropriate volume. The sequence of opening and closing the pistons will dispense that volume. Another method is to use an auger screw inside a tube which can be driven by a motor. These valves are usually specific to a limited range of deposit size or to certain viscosities.
Endless-Piston-Principle®2
Recently, a pump technology which delivers positive displacement, volumetric dispensing or dosing has been applied to the precision application of industrial materials, and which can deliver as little as 0.1 μl. A progressive cavity pump is a type of positive displacement pump. Typically, it consists of a single-helix metal rotor and a double-helix hole in an elastomeric stator. The rotor seals against the stator, forming a series of spaces or pockets, which translate along as the rotor rotates, keeping their form and volume. The pumped material is moved inside the pockets. In addition, the pockets are shaped such that they taper and overlap; the output is continuous, even and non-pulsing.
The flow rate is directly proportional to the rate of rotation (which can be reversed), and the volumetric output of the pump is directly proportional to the number of rotations. Due to the rotor/stator seal, input pressure has no effect on the pump, so it achieves true positive displacement. It is also able to pump at very low rates, and low levels of shear are applied to the pumped fluid.
Precision Dispensing
Dispensing or dosing units based on this technology are available for precision applications. They consist of the rotor/stator assembly and a motor drive unit, in a pen-like configuration. A separate controller allows programing of the motor – speed and number of rotations to effect dots or deposits of specific volumes, or continuous beads. At the conclusion of a dispense, the motor can be reversed briefly to prevent stringing or dripping. A dispensing needle is fitted to the end of the pen using a standard luer fitting.
Crucially, once a material has been characterised, a desired volume can be selected on the controller, which is dispensed regardless of material viscosity changes and independent of ambient temperature. The technology handles viscosities from water up to very high viscosity pastes, including abrasive, filled or shear-sensitive media. Flow rates range from ~ 0.1 to 60 ml/minute. The pen can be hand-held or fitted to automation.
Applications
The benefits of the continuous, volumetric positive displacement pump include precise, process stable dosing or dispensing, which is benign to the media. Control is linearly proportional, so is simple to program – and very repeatable and consistent. With automated handling, the highest precision of at least ± 1% and reproducibility over 99% of the medium is achieved. Dispensing a bead is accomplished by setting one parameter – the volume flow; matched to the speed of a robot or other automation, it is possible to dose coherent beads down to a width of 250 μm and at traverse speeds of up to 300 mm/s.
The same technology has been applied to metering and mixing two component materials; two pumps supply the components to a static mixing nozzle in the correct volumetric ratio. It has found applications in optics & photonics, biochemistry, photovoltaics, electronics and semiconductor manufacturing and medical technology.