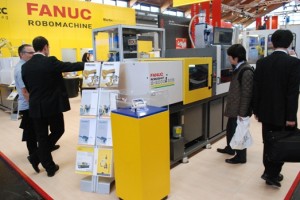
During the last few years, injection moulding processors have shown increased interest in electric injection moulding machines (eIMM) with, on the one hand, their high energy economy and awareness of fully automatic production systems on the other. At Fakuma 2012, in Hall B3, Stand 3211, FANUC ROBOMACHINE DEUTSCHLAND GmbH will be ex-hibiting three electric ROBOSHOT IMMs, thus seamlessly staying abreast of emerging user demands.
Live Demonstrations: A 30-ton ROBOSHOT, integrated into a fully auto-matic manufacturing cell, will be producing highly precise miniature components (gears for watches) by micro injection process. In addition, visitors can obtain information about economic production of two-component parts (ice scrapers) on a 150 ton ROBOSHOT machine. Responsible for the second component, is a Mould-Masters E-Multi injection unit. Finally, a new 100-ton ROBOSHOT Alpha-S-100iA – with a more powerful control system – will produce components for protective helmets precisely and highly economi-cally.
“These three applications show a cross section through the FANUC ROBOSHOT performance …”, says Sales Manager Rainer Zerr (photo) and explains “ …with energy recovery control, sta-ble repeatability and process security, Precise Metering Control – PMC 2 and 3 – and Backflow Monitor as well as the efficient AI mould protection. Last but not least, we demonstrate together with our systems partners, economic and technical competence in the areas of two-component injection moulding and manufacturing cells with high flexibility.”
Manufacturing cells for micro injection moulding applications
On a FANUC ROBOSHOT S-2000i-30B (300 kN clamping force), micro parts – tiny cog wheels for watch movements – are being produced. A 6-axes robot, FANUC LR Mate 200iC, including a visual inspection system supplied by systems partner ROBOTEC, removes and deposits the fin-ished components. Result: 100% visual inspection of both sides of the parts, consistent parts weight of 0.004 gram POM, accurate product dimensions (outer diameter = 3.2 mm, shaft di-ameter = 0.3 mm), and weights are within the range of tolerance, i.e. +/- 0.2 percent.
Two-component application in the manufacturing cell
The coordinated cooperation with Mold-Masters Europa GmbH proves to be flexible and eco-nomic in conjunction with two-component applications. A FANUC ROBOSHOT S-2000i-50B (500 kN clamping force), operating with an E-Multi as second injection unit, is complemented with an integrated rotary drive and a flexible injection unit support. The two-component mould, supplied by POLAR-FORM Werkzeugbau GmbH, Lahr, Germany, produces ice scrapers in PS and TPV. Part extraction and printing is accomplished by a FANUC industrial robot in the manu-facturing cell designed by systems partner MARTIN MECHANIC.
New FANUC ROBOSHOT Alpha-S-100iA produces protection components
New! Integrated and synchronized material supply into the IMM feed zone: this ensures optimum material venting. Bicycle helmet components for inside diameter setting are made in POM in a two-cavity mould supplied by DHG Knauer: part shot weight is 24.3g. Products such as these must adhere to stringent safety standards. These parameters require a very high process stability and reliability. The fully electric FANUC ROBOSHOT injection moulding machine complies 100% with these requirements. A linear handling unit incorporating FANUC servo drives, supplied by Hi Tech Automation, extracts the finished parts.
Fundamental energy saving
The ROBOSHOT electric IMM operates with extremely low energy consumption. Its control monitor indicates the actual power consumption and regenerated power in a graphical and a numerical display. Also, the accumulated power over a specified period, the trend of power con-sumption and power demand are displayed. Energy savings are realized by the following fea-tures: FANUC’s superior motion control technology for high efficiency, power recovery, and insulation of the heating zone.
The feature of energy recovery – whereby the servo-drive motors in the ROBOSHOT machines generate electrical energy as they decelerate, when closing and opening the mould after locking – contributes a tremendous potential for reducing energy costs. “We utilize kinematic and turn it into regenerated power instead of discharging thermal energy into the air,” says Wolfgang Haak, Applications Engineer at FANUC, and adds that “the amount of energy produced in this way de-pends on the machine and process, but it amounts to around 10 percent of power saved on av-erage, on top of the 40-60 percent lower energy consumption of electric machines as opposed to hydraulic ones.
Today, we must not forget the issue of CO2 emissions: the greater the energy requirements of a manufacturing plant, the higher are the CO2 emissions. With our ROBOSHOT machines, less energy is required from the national power grid, which means lower emissions and the protection of our environment”.
Moving on to the control system used by the ROBOSHOT IMMs, Wolfgang Haak points to the actual energy displayed in KWh on the control system screen. He added: “The customer doesn’t have to take a specific external energy measurement. The FANUC system is the most effective transparency tool for customers with regard to their energy balance.”
FANUC ROBOSHOT Highlight at a glance
Sustainable process capability – stable moulding through Backflow Monitor and Precise Metering Control PMC2&3: The behaviour of melt in the cylinder is detected and shown on the screen. The first feature is the Backflow Monitor which shows the backflow of material at the time of in-jection on a screen. This allows conclusions (feedback) regarding the stability of the injection, the closing characteristics of the non-return valve as well as its status. The second feature is the Precise Metering Control (PMC2&3). Residual pressure in the screw flights compensates volume displacements at the end of the dosing cycle. It guarantees a constant dosing volume and minimizes weight deviations of the parts to be moulded.
The AI mould protection and AI ejector functions of the FANUC ROBOSHOT series of IMMs are very effective in safeguarding a longer lifetime of the mould. The AI mould protection function stops the platen motion instantaneously as soon as it detects foreign parts or obstacles remaining in the mould – thus preventing damage to the mould. It also averts damage to the slide core and inserts when the mould is opened. Furthermore, the AI ejector function is very effective in preventing damage to the ejector when it moves forward or backwards. The machine reacts be-fore damage can occur at the mould, as soon as an ejector’s movement starts to stiffen up.