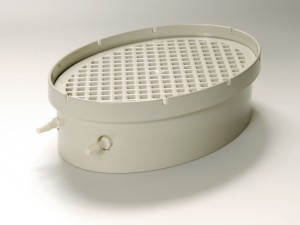
Riding growth rates of 30% a year, Biorep Technologies (Miami, FL) is adding injection molding capacity as it accelerates a plastics-for-metal strategy for its proprietary medical devices and instruments.
Biorep now operates three injection molding machines: two 110 Mitsubishis and one 15-ton Nissei. One of the Mitsubishis was purchased at NPE2012 in Orlando, FL. “We’re evaluating the possibility of adding more injection molding machines, but we have not made a decision yet,” Felipe Echeverri, engineering director for Biorep Technologies, told Plastics Today in an interview.
Biorep Technologies began operations in 1995 as an engineering partner with the Diabetes Research Institute (DRI) in Miami. Ramon Poo (pronounced Poe), a mechanical engineer who operates a plastic bottle business in Miami, started Biorep after his daughter was diagnosed with diabetes.
Poo met with Dr. Camillo Ricordi, DRI’s scientific director, and discovered an opportunity to design and manufacture equipment that would allow advanced-stage diabetics to receive transplants and live insulin-free. Projected production volumes for the equipment were too small to interest major medical device manufacturers.
Biorep’s original manufacturing focus was on equipment used to isolate islet cells from the pancreas now known as the Ricordi Chamber. They were produced in very small quantities with parts made in the company’s machine shop and donated to DRI. Poo received numerous humanitarian awards for his work.
The Ricordi Chamber was originally produced from stainless steel, which was difficult to shake during the isolation process and didn’t allow visual analysis of the process. In one of the company’s first major shifts from metal to plastics, the Ricordi Chamber was injection molded from Ultem HU polyetherimide (PEI) resin, a translucent, high-temperature, autoclavable plastic.
The transfer to plastic also allowed the company to move toward mass production, necessary to reduce costs.
Biorep also developed a perifusion system used for testing pancreatic islets in-vitro. It solved two major challenges in cell secretion analysis: throughput and repeatability. It is an automated system that stimulates different cell types with total environmental control and the collection of its secretions according to programmable protocols.
Expanded product line
The company has since grown and its focus has expanded into cardiac surgical instruments.
Biorep is now also partnering with Dr. Joseph Lamelas, chief of cardiac surgery at Mount Sinai Medical Center, in a company called Miami Instruments, which develops devices for minimally invasive heart surgeries. It’s called the “Miami Method” and the instruments are distributed exclusively by Medtronic, the medical device powerhouse based in Minnesota.
The original design for the Joseph Lamelas Knot Pusher and the Visor support bracket and S-Blade of the Joseph Lamelas Atrial Lift System called for stainless steel.
At a recent MD&M West, Echeverri came across a potential substitute at the Solvay Specialty Polymers booth: Ixef polyarylamide resin, which has tensile and flexural strength similar to many cast metals and alloys at ambient temperature.
Plastics improved the Ricordi Chamber. (Sabic)
“Ixef PARA’s strength and rigidity is similar to stainless steel and it can also be molded, allowing us to eliminate machining and realize a major cost reduction over stainless steel,” said Echeverri.
The molded black parts also reduce light reflectivity for the surgeon. They also can be sterilized with gamma ray radiation without any significant change in appearance or loss of mechanical properties.
Biorep is also developing other surgical instruments and is considering Ixef PARA resin for a range of metal replacement uses.
Biorep had primarily relied on its own machine shop to make prototypes and production parts. Biorep also sourced parts and prototypes from Proto Labs (Maple Plain, MN). The new injection molding machinery give the company more capacity and flexibility, Echeverri, said in the interview.
Other plastics used by Biorep Technologies include ABS from Sabic, PBT-type polyester from Ticona and copolyester from Eastman.