A critical single-use consumable product for the DxI 9000 analyzer is the highly sensitive polypropylene (PP) pipette tip. This pipette collects a patient’s sample from a test tube and dispenses it into the analyzer. This critical step requires pipettes to remain undamaged to ensure the quality of the analysis. The Beckman Coulter Diagnostics Global Plastics Team needed a packaging solution seamlessly integrated with the DxI 9000 IA analyzer, minimising material content and capitalising on recycling opportunities.
Beckman Coulter approached Plastic Ingenuity (P.I.) to partner on designing a custom thermoformed package to hold and protect 520 pipette tips in four rigid polystyrene trays
Thermoforming process – overcoming the design challenge
The thermoforming process differs from the injection moulding process. It is a manufacturing process where a plastic sheet or film is heated in an oven to a high enough temperature so that it can be stretched into a mould that is formed and cooled to a specific finished shape in a mould (or die) and trimmed to create a usable product. Thin-gauge thermoforming (Fig. 2) is primarily used to manufacture containers, lids, trays, blisters, and clamshells for the food, medical, and general retail industries. To protect the highly sensitive pipette tips from handling damage, P.I. designed a unique cover and base tray to be as robust as possible yet remain a viable thermoformed PET part.
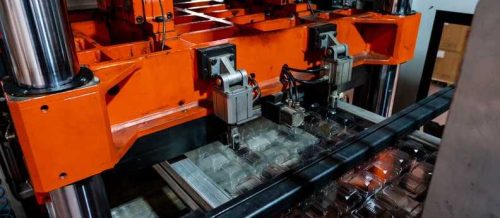