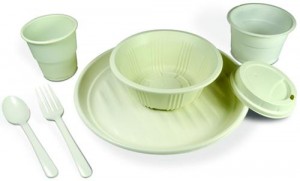
Although bioplastics are still a very small part of the plastic waste stream, some manufacturers are talking to recyclers about developing recycling processes for their products. NatureWorks, for example, is working with the Association of Post-Consumer Plastic Recyclers to help develop mechanical and chemical recycling processes for its Ingeo materials, as well as end-markets for the recycled plastic, Steve Davies, global director of marketing and public affairs, told us.
Non-recycled petroleum-based plastics are a big problem in landfills. If left untreated, they don’t biodegrade for a long time. And if not recycled or converted to fuel or electricity, the energy they contain is wasted. Estimates of how much plastic goes into landfills vary depending on who’s measuring, but according to the EPA, only 12 percent of US plastics got recycled in 2010.
Bioplastics end-of-life solutions are composting or recycling, depending on whether it’s single-use or durable. “Composting plastic turns it back into the CO2 and water it started as, which closes the cradle-to-cradle loop but doesn’t give an opportunity for re-use,” said Davies. “This makes sense in compostable food packaging and food serviceware. Since no one sorts the food waste from the plastic waste for recycling, it all goes to the landfill anyway, where compostable materials can biodegrade. Many food serviceware plastic makers now have a compostable version.”
Durable bioplastics aren’t compostable, and are harder to recycle than single-use bioplastics, Kent Furst, industry analyst for the Freedonia Group, said in an interview. “First, they are often made durable by adding reinforcing agents and fillers, and these can interfere with the recycling process. Second, sometimes the bioplastic is made durable by being blended with conventional plastics, and it becomes difficult to separate the materials for recycling.”
Actually, most higher-performance engineering plastics are tough to recycle, bio-based or not, because of the potential for contamination, which can drastically reduce the recycled resin’s desirable properties. “So special handling, such as for scrap, is required for high-performance plastics if they are to be recycled into a material that has properties similar to the original,” said Furst. “These guidelines for special handling and processing must be made available to recyclers. Some durable bioplastic vendors are addressing these problems by providing the relevant information to their processor customers.”
“Whether it’s crystallized or blended with other polymers, if handled appropriately like other polymers, Ingeo can be recycled and its properties retained through numerous recycle events,” said Frank Diodato, segment director for durables and distribution for NatureWorks. “This is true for both post-industrial and post-consumer Ingeo (engineering) plastics formulations. At the post-consumer level plastics are often mixed, making recycling more difficult, but that’s not as common with post-industrial materials.”
Although bioplastics have been targeted as “contaminating” the recycling and waste stream, nearly all plastics do, said Davies.
“Bottles in the US are typically made of either 100-percent clear polyethylene terephthalate (PET) or 100-percent white high-density polyethylene, so these are easily identified. They are easy for consumers to identify, and for material recovery facilities (MRFs) to sort manually, and therefore get recycled in very high numbers. By contrast, clear clamshells can be made of PET, polystyrene, or polypropylene, and recyclers need the most modern equipment to distinguish among them. Most of them sort out bottles only and then landfill the rest, or ship it to Asia for sorting, or ship it to end users here for reuse.”
Aside from sharing details with MRFs about how to work with its products, NatureWorks also wants to help develop end markets. “Once there are end markets for a material, the MRFs will be happy to sort it.” said Davies. For example, traditional plastics compounders buy different plastics feedstocks and mix them together to make value-added blends. Some of them are interested in buying NatureWorks’ recycled polylactic acid (PLA) bioplastics. BioCor, for example, already buys post-industrial and post-consumer PLA scrap, both petro-plastic and bioplastic.
Source : www.designnews.com