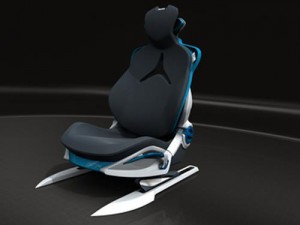
Plastics and chemical giant BASF and automotive supplier Faurecia have co-developed a car seat backrest that integrates the seat frame and back panel into a single structure. The composite backrest reduces the need for foam, eliminates metal almost entirely, and simplifies — read shortens — the trimming process. It also saves weight.
The concept Performance Seat, along with a concept 100-percent plastic wheel made of BASF’s impact-resistant polyamide Ultramid Structure material, were displayed at the recent North American International Auto Show in Detroit. Paris-based Faurecia already demonstrated the Performance Seat at the LA Auto show in November.
Aimed at smaller and midmarket vehicles, the Performance Seat weighs 20 percent less than conventional seats made with steel frames and is 30 percent thinner. It is also designed with esthetics in mind: Its materials were inspired by sportswear and fashion design.
The outer frame’s composite material consists of nylon, continuous glass-fiber reinforcement, and a metal recliner adapter combined via an injection molding process. It provides the necessary support to pass crash tests and contains a thin, flexible seat area within the industry’s first “compliant shell,” consisting of the back panel. This shell conforms to differing body sizes, shapes, and postures of driver and passengers by changing as people move in the seat. The shell was inspired by office furniture with flexible thermoplastic support. Instead of being covered and hidden by foam and fabric, the structure is exposed to view like an architectural element. The eliminated material further reduces space and weight.
The compliant shell eliminates 75 percent of the foam used in today’s cushioning in car seats. In addition to the backrest, the Performance Seat includes a plastic cushion module, which Faurecia co-developed with Rhodia SA.
A thin pad of foam and fabric covers both the backrest and the plastic cushion module. Faurecia bonds the fabric to the foam using a technology called “cover carving,” which enables the creation of complex and unique shapes that are difficult to produce with more conventional trimming methods. Along with its bonded fabric cover, the foam pad in the backrest measures 15mm. The cover and foam are installed directly on the compliant shell, snapped on with retainers. The combination of bonded fabric and foam is used only in areas where the driver or passenger’s body actually touches the seat, so no foam or trim is wasted.
Faurecia reportedly expects to begin mainstream production of its all-composite Performance Seat backrest as soon as 2014.
Source : www.designnews.com