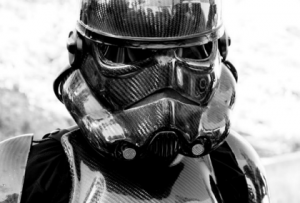
A UK consortium has launched a new family of yarns and fabrics made from recycled carbon fibers that offer properties rivaling those of virgin carbon fibers but cost less.
The six consortium members — Advanced Composites Group (part of Umeco Composites Structural Materials), Exel Composites UK, NetComposites, Sigmatex, Tilsatec, and the University of Leeds — debuted the family of materials at the recent Composites Engineering Show in Birmingham.
The materials are the result of the consortium’s recently concluded FibreCycle collaborative project, which developed technology for recovering waste carbon fibers, blending them with resins such as PET, and converting them into different types of materials. It recovered carbon fiber from all stages of manufacturing, and it developed reprocessing techniques within a representative supply chain.
The new carbon-fiber materials are continuous, highly aligned reinforcements, including yarns, woven textiles, noncrimp fabrics, prepreg tapes, and preconsolidated sheets. Like other commingled and blended materials, the fabrics are molded under pressure and pass through a heating and cooling cycle. Several demonstrator products, including press-molded automotive parts, have been produced. The commercial members of the consortium serve multiple industries, including automotive, aerospace, and industrial.
Composite laminates made from 50 percent recycled carbon and 50 percent recycled PET, measured by weight, can deliver at least 90 percent of the tensile modulus, or stiffness, and 50 percent of the tensile strength of an equivalent composite made from virgin fibers.
“The properties achieved mean that” the materials are “suitable for many applications, especially in the automotive, aerospace, sports and leisure, medical and energy sectors,” Dr. Sophie Cozien-Cazuc, FiberCycle project director and collaborative R&T project manager for Umeco Composites Structural Materials, said in a press release. Though these new fibers and fabrics have almost the same stiffness as virgin materials, the carbon-fiber feedstock on which they are based costs less than virgin fibers and fabrics would.
As the volume of nonbiodegradable carbon-fiber-reinforced plastics (CFRPs) grows worldwide, there is also a growing concern in the UK composite industry about the huge amounts of waste generated by both manufacturing processes and end-of-life products themselves. Thermoset CFRPs, such as those produced with materials from the FibreCycle project, are usually recycled using one of three different processes: pyrolysis, solvolysis, or fluidized bed.
Pyrolysis, which can be either a continuous or batch process, involves burning off resins with a very limited amount of oxygen. Recycled fibers can be sold in milled, chopped, or pelletized form. Microwave pyrolysis processes are also being developed in the US, Germany, and the UK.
During solvolysis, both the resin and the fibers are recovered. High temperature and high pressure are required to reach a supercritical state, and the process uses fluids such as water, propanol, or methanol.
In the fluidized bed process, both cured and uncured composite wastes are fed into a bed of sand and exposed to hot air, which breaks down and vaporises the polymer. The resin products are fully oxidized in a combustion chamber, where the heat energy can be recovered. Fibers and filler are carried out of the bed by way of the gas stream.
Source : www.designnews.com