KraussMaffei Berstorff of the Germany-based KraussMaffei Group will present the new Schaumtandex ZE 40 / KE 90 machine for foaming processes at K 2013.
“Due to their high consumption of raw materials and energy, existing production machines are not economical for testing new processes or modifying process parameters,” said Hilmar Heithorst, Divisional Manager Sheet and Foam Extrusion Lines at KraussMaffei Berstorff. “Even at low speeds when the test results can only be transferred to a limited extent, our production machine quickly consumes a few hundred kilograms of material.”
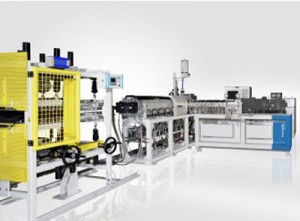
The melting extruder, a ZE 40 UTXi twin screw extruder, can be individually configured through the modular design of barrels and screws in order to process formulations with up to 10 different components. With regard to melting, the modular process concept of the ZE 40 UTXi offers ideal conditions for processing all standard plastics and numerous high-temperature plastics up to a maximum temperature of 350°C, says KraussMaffei Berstorff.
Liquid, environmentally-friendly propellants are injected directly into the processing zone via injection nozzles and are mixed homogeneously in the plastic melt. Thanks to the C clamp housing connections and the compact design, the processing unit in the ZE 40 UTXi can be easily converted in order to change the formulation.
The specially designed KE 90 single-screw extruder for melt cooling cools the melt containing propellants down to a temperature just above the solidification point. Active melt sealing prevents the propellants from leaking into the gearbox. The special geometry of the screw ensures optimum melt cooling through modern calculation and simulation methods at low drive power. Energy consumption is said to be reduced by 30-40%.
“Melting and cooling extruders are optimally coordinated to optimize the cooling effect and quality, even with maximum output, high propellant content, or sophisticated formulations,” said Mr. Heithorst.
The Schaumtandex machine is equipped with a control cabinet and a 19″ monitor as standard features. According to KraussMaffei Berstorff, all control functions can be triggered by simply pressing a button. The entire operating concept is intuitively designed and is easy to understand. The large monitor provides a total overview of the extrusion process and the machine functions.K 2013 will be held from October 16-24 in Düsseldorf, Germany.
Source: www.adsalecprj.com/Publicity/MarketNews/lang-eng/article-67007262/Article.aspx