KraussMaffei will present its machine and processing technology involving components made from fiber composite materials and polyurethane at PU China 2013.
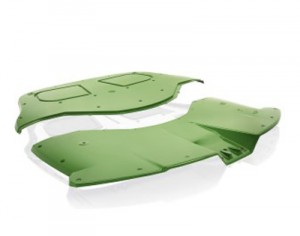
“Today our machine and mold technology portfolio encompasses everything from injection molding short glass fiber reinforced parts to high strength lightweight components with a complex mesh structure in a reactive matrix,” explains Erich Fries, Head of the Composites/Surfaces Business Unit of the Reaction Process Machinery segment at KraussMaffei.
For PU China, the company is showing various examples of components made from fiber composite materials that are not only solid and lightweight, but can be manufactured with the surface quality needed for product components with high visibility.
The long fiber injection (LFI) process is particularly suited for large components for trucks and agricultural machinery, introduces KraussMaffei. This process involves introducing a mixture of long glass fibers and polyurethane resins (PUR) into an open mold using robot control. After closing the mold, the mixture reacts to create the finished component. A GRP roof module for a harvester and an instrument panel manufactured this way will be on display.
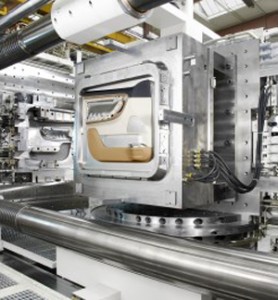
In addition, the resin transfer molding (RTM) method will be presented using a roof module for a sports car. Resin transfer molding is used to implement lightweight fiber reinforced components for high safety requirements, according to the company. It requires inserting preassembled fiber mesh into the mold, then closing and evacuating the mold. Each fiber is wetted without creating entrapped air via the subsequent injection of reactive resin into the cavity. Since this component is in the visible area of the vehicle, the surface is provided with a high quality carbon appearance.
The clear coat molding (CCM) process, where wood parts are coated with transparent PU to attain outstanding visual characteristics, is being presented alongside the SkinForm process for finishing thermoplastic molded part surfaces, which have great appeal due to their appearance, leather-like feel and resistance to scratching. SkinForm is a multi-component process where the thermoplastic carrier is manufactured first and flooded with PU in part or over large areas in a second step.
KraussMaffei has already established a partnership with Guangzhou Echom Technology Co. Ltd, a supplier for the Chinese automotive industry. A SkinForm system is currently being installed at the company’s headquarters in Guangzhou. It will be available for trials and small-scale series production after the trade show.
“Our innovative cross-process procedure reduces the costs of manufacturing high quality component surfaces by 30% compared to conventional multi-stage processes. Our expertise lets us provide the process best suited for specific component requirements,” emphasizes Mr. Fries.
PU China will be held from September 10-12 in Nanjing, China.
Source: www.adsalecprj.com/Publicity/MarketNews/lang-eng/article-67007010/Article.aspx