ENGEL combines the best of two worlds in the new ENGEL e-speed 650 injection moulding machine. The new high-speed machine uses the tried-and-tested technology of the all-electric ENGEL e-motion and ENGEL e-cap high-performance series and also boasts the performance of the ENGEL speed series, meaning it unites outstanding injection speeds with maximum energy efficiency.
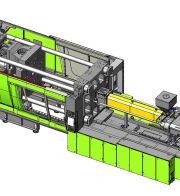
Two aspects were focused on in particular during the development of this addition to the ENGEL speed series, which is a proven high-performance toggle clamp series of machines. They were the introduction of higher clamping forces at the top end of the series and a new drive concept which guarantees excellent energy efficiency levels even at high speed.
The result is a 650-tonne hybrid machine with an electric clamping unit and a completely new drive solution. As power peaks are traditionally not achieved economically when high clamping forces are combined with short cycle times, a flywheel acts as an electric reserve in the new ENGEL e-speed. It stores the braking energy from the platen movements and transfers this energy back to the motor as and when it is required for processes such as the reacceleration of the clamping movements.
This ensures that the power requirements of the drive motor are covered. When the storage capacity is reached, the excess energy from the generator is fed back into the network and not converted into heat by the braking resistance – which is what usually happens with older machines. The ENGEL e-speed 650 is therefore able to run with a relatively low and above all constant connected load. Power peaks are reliably avoided. Ejection movements are also executed electronically on standard models.
A hydraulic variation is available as an option.On the injection unit side, the ENGEL inline injection unit, which has particularly high injection dynamics and an electric plasticising drive, is used, which enables injection speeds of up to 800 mm per second to be reached. Screw diameters 80 and 90 are available with the ENGEL e-speed 650 at the outset.
Thin-wall injection moulding with ultra-short cycle times
As is the case with all ENGEL’s toggle clamp machines, the toggle clamp on the e-speed 650 is encapsulated, which ensures that oil consumption levels are well below average. Thanks to this special design principle, the machine achieves extremely short dry cycle times. The integrated controlled spindle cooling system also helps to shorten cycle times, which can be less than four seconds when thin-walled items like containers and lids are being manufactured for purposes such as food packaging.
The ENGEL e-speed 650 has been specially equipped with an extensive range of options (including cooling water and pneumatic options among other things) to enable it to meet demanding packaging requirements. In addition, its particularly long opening stroke allows it to work with large stack moulds without any problems.
Another development aspect was also heavily focused on when the new hybrid machine was being designed. To make it easier to access the mould area, the safety gate was constructed in two parts. In the case of minor manual interventions, the machine operator is able to access the mould area quickly and easily with just one hand, and only has to open the safety gate completely when the mould needs to be changed.
ENGEL’s new hybrid machine will be demonstrating its impressive performance levels at the K trade fair in Düsseldorf from 16th to 23rd October 2013. At ENGEL’s stand in hall 15, an ENGEL e-speed 650/90 will be making thin-walled containers in an 8+8-cavity stack mould in a total cycle time of under four seconds.
Source: http://www.engelglobal.com/engel_web/global/en/22_4610.htm