Three prototyping programs indicate strong potential for injection molded amorphous metal in medical device applications.
“There’s a tremendous amount of interest from the medical community,” Tom Steipp, CEO of Liquidmetal Technologies (Rancho Santa Margarita, CA) said in an interview with Plastics Today.
Selling points for molded amorphous metal include:
- Compact size and ergonomic shape,
- Production costs in line with plastic injection molding,
- Strong material with thin walls,
- Corrosion resistance, and
- Non-magnetic (MRI compatibility).
Steipp said in the interview that the full biocompatibility of the amorphous metals’ technology is still being tested, “but nothing to date indicates that will be a problem.”
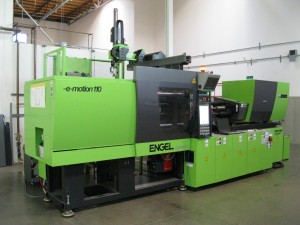
Liquidmetal is a unique material developed at the California Institute of Technology in the early 1990s.After conventional alloys cool to a solid state, they generally crystallize into geometric types of structures that have built-in weak points. Liquidmetal has an amorphous, liquid-like atomic structure in its solid state, making them significantly stronger. The technology has struggled, but received a significant boost within the last 15 months due to a breakthrough injection molding machine developed by Engel.
The company has already signed licensing agreements with Apple and Swatch to raise much-needed cash, and is now actively working with potential customers on several prototype programs in the oil & gas field, sporting goods, and other fields as well as medical.
The specific immediate targets are parts that are currently made from machined metal or injection molded metal powder. One example would be jaws for surgical instruments.
“MIM is a lower cost technology. The difficulty is maintaining tight tolerances in three dimensions,” Steipp said. “We can hold tolerances of plus or minus one to two thousandths over three to four inches. MIM holds plus or minus three thousandths per inch.”
One advantage of using a processing technology closer to plastics molding is that more complex parts can be designed, allowing parts’ integration, increased functionality and reduced secondary processing.
“If our goal was to take a machined part, or even a MIM part, and make it out of liquid metal, the process would go faster. What you find is that a part designed for injection molding is different than a part designed for machining or MIM.”
One company exploring the possibility of using amorphous metal in a medical device is an Israeli company called Medinol, which makes cardiology stents that are distributed by Cordis, a Johnson & Johnson company. Its stents are currently made of conventional metals such as stainless steel, cobalt chromium, and NiTinol.
A Medinol patent approved in February describes an expandable helical stent made from an amorphous metal alloy that is formed from flat or tubular metal in a helical coiled structure which has an undulating pattern.
ConforMIS, Inc. (Burlington, MA) references potential use of Liquidmetal in several recent patents for surgical tools for arthroplasty.
Dr. Jacob (Kobi) Richter, co founder of Medinol, was also awarded a patent through a company called Zulu Holdings for “a new class of medical devices and implants comprising amorphous metal alloys.”
Source: http://www.plasticstoday.com/articles/injection-molded-liquidmetal-targets-mim-machined-parts0529201301