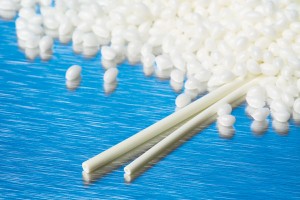
Parker Hannifin Corp., a major consumer of plastics for its motion and control businesses, is launching a major bid to become a player in specialized medical plastics.It has created a medical grade polyurethane that demonstrates polycarbonate resistance to oxidation and alcohol swelling, and is also said to possess improved resistance to environmental stress cracking. The material is polymerized by the Parker Engineered Polymer Systems (EPS) Division in Salt Lake City, UT.
“We have been in the urethanes since the 1960s, but we typically haven’t sold them, we used them in our seals,” said Justin Smith, EPS Life Science Market manager told PlasticsToday in an interview. More recently, Parker has made a concerted effort to use its expertise in urethane chemistry and manufacturing as a beachhead into the medical market.
The new product, called Parker Medical Grade ALC Polyurethane, is aliphatic polycarbonate-based thermoplastic polyurethane. Smith said that ALC polyurethanes are non-yellowing, color-matchable, and are available in clear or radiopaque grades.Applications include vascular access devices, cardiovascular treatment devices, disposable surgical supplies, tracheotomy devices, urological devices, dialysis devices, and feeding tubes.
“Many medical-grade urethanes, including ALC polyurethane, are now made with aliphatic polyurethane instead of the old standard, aromatic polyurethane, because of yellowing and carcinogenic concerns,” said Arlo McGinn, Parker EPS senior chemist. “The aliphatic polyurethanes have lower mechanical properties than aromatic but degrade to potentially safer end products, do not discolor upon exposure to light, and also show enhanced resistance to hydrolytic decomposition. However, along with the decreased mechanical properties, aliphatic polyurethanes are more prone to a physical degradation process-termed environmental stress cracking-than their aromatic counterparts.”
Parker has a proprietary formulation and also says it uses advanced manufacturing processes.”We analyzed the performance of several aliphatic polycarbonate urethanes, including our ALC polyurethanes and two competitors. Upon exposure to alkaline conditions, differences in tube performance within the ALC class were compelling: the competitive ALC urethane tubes quickly degraded and failed due to the effects of environmental stress cracking. During the same time period, however, Parker’s ALC formulation showed no significant change after initial softening over the course of the testing, and demonstrated enhanced resistance to environmental stress cracking.”
They may be extruded as well as injection molded. Extrusion configurations can be single lumen or multi lumen, as well as tapered (bump) or coextruded.Expanded capabilities include ISO Class 7 and Class 8 cleanroom manufacturing. Registrations include ISO 13485 and ISO 9001.The new grade will be the first in a series of medical-grade polyurethanes. “Our plans are to launch aromatics, aliphatics and then polyethers and polycarbonates,” Smith said in the interview.Important producer of medical-grade polyurethanes include Lubrizol, Bayer MaterialScience, DSM, and Teleflex.
Source: http://www.plasticstoday.com/articles/parker-expands-role-medical-polyurethanes0423201301