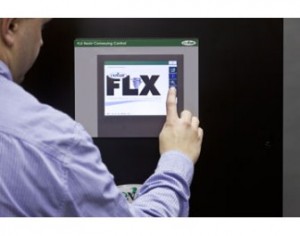
At the recently concluded Plastec West 2013, The Conair Group demonstrated the remote control capability of its FLX material-handling control system by interfacing the system back in the company’s Pennsylvania Technical Center with a laptop computer. The FLX material-handling control system, which was recently expanded to handle up to 128 loaders and 40 vacuum conveying pumps, is a simple, entry-level plastic-resin-conveying system that can be connected to the internet and Ethernet. It can communicate with any Internet-connected device and is easy and inexpensive to install and expand.
With the internet connection, all the functionality of the touch-screen FLX control panel is replicated on the remote laptop, explains Conair. Changes to settings, responses to alarms, troubleshooting and other operations can be completed from anywhere. In addition, up to six remote interface units can be installed in the plant and connected to the system via Ethernet.
The FLX was designed to be affordable and easy to install and expand. A system can be started with just 8 loaders and 2 pumps (one primary pump and one back-up pump), and capacity and capabilities can be increased in manageable increments when necessary, simply by adding input and output cards.The system can also include high-level functions as multi-source/multi-destination loading, purge, ratio loading, ratio loading with purge, reverse conveying for regrind recovery, loader fill sensing and much more. Loader demands for material are handled on a first in/first out (FIFO) basis.
According to Conair’s explanation, most other controls simply poll every loader sequentially, which means some loaders may actually run out of material before they can be filled. With the FLX control, however, demands are filled in the order received. Any loaders on any pump can even be given priority status, becoming the next receiver filled regardless of what other demands may exist in the system. When configured for ratio loading, the control can be programmed to load either virgin or regrind first. Layering sequences can be calculated automatically or manually.
The PLC-based system has a 191mm color touch screen as the standard operator interface with a 380mm color touch screen available as an option. The graphical display is easy to read and easy to use. Color-coded icons let operators know the status of connected equipment at a glance. Any interruptions to optimum processing are clearly signaled for fast resolution with no nuisance alarms. Alarms can be programmed as active (disabling the device being alarmed) or passive, allowing operation to continue until maintenance staff can identify the problem. Built-in help screens simplify troubleshooting. Plastec West 2013 was held from February 12-14 in Anaheim, California, the US.
Source: http://www.adsalecprj.com/Publicity/MarketNews/lang-eng/article-67002702/Article.aspx