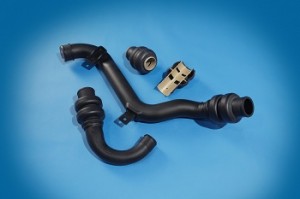
Injection and blow molding combine in the production of a resonator molded from polyamide materials. The internal (ID) section injection molded in the first step is then overmolded to form the external (OD) section via blow molding. The resonator is used in 2012 model Ford Fusion and Escape models using the OEM’s 2.0-L Ecoboost engine.
System supplier Contitech AG (Hannover, Germany) selected a 20% glass filled grade of Nylon 66 (Zytel 70G20HSLX) from DuPont Performance Polymers (Wilmington, DE) for the ID and a 35% glass filled for the OD (70G35HSLX) to become one homogenous structure upon cooling. The first proto-type design for the plastic resonator used two dissimilar polymers, polyphenylene sulfide (PPS) on the ID and Zytel on the OD.
Processing was handled by Polymer Products (Grand Rapids, MI). Particular attention was required for design of the die/tooling to permit the parison to enter concentrically over the previously injection molded ID structure and remain centered in the blow molded OD upon cooling.The resonator was originally constructed of stainless steel. A 30% weight saving was achieved by switching to plastics, while direct cost saving associated with the application was also pegged at 30%.
Performance enhancements have also been gained through the switch to polyamide. Noise, vibration and harshness (NVH), for example, has been reduced in the plastic resonator due to the elimination of blow-by/leakage between the stainless steel chambers in the stainless steel resonator. As a result of the reduced weight and a better functioning design, improved gas mileage is also expected.
Source- http://www.plasticstoday.com/articles/injection-blow-molding-combination-delivers-nylon-polyamide-pps-stainless-steel-20130211a