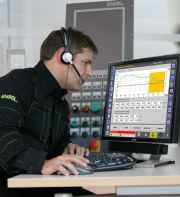
A machine standing still can soon become expensive. Recognizing and solving the problem quickly and competently is then called for. To do so, ENGEL links the injection molding machines at its customers’ factories with more than 300 service engineers and its worldwide production plants via the ENGEL e-service.24 service package. This ensures the shortest response times – around the globe and around the clock.
ENGEL never sleeps. Eight production facilities on three continents let the service team of ENGEL e-service.24 be available 24/7. Using a remote connection, the specialists of the injection molding machine manufacturer can start looking for the cause as soon as an error message appears. The highlight: the injection molding machine will request help on its own. In the event of a failure, or for service purposes, the system will automatically inform the qualified personnel and machine operating staff by e-mail. They can forward the error or service message directly to the experts at ENGEL as a request.
If necessary, the ENGEL service engineers will give the customers instructions and explanations by audio, video or text conferencing. Document sharing functions and redlining tools make efficient cooperation possible across thousands of kilometers. The original screen pages of the machine controller can be viewed over the Internet. Because data access is done in real-time, the current state of the machine can be displayed whenever needed. VNC conferences and remote desktop provide access to remote systems. Many problems can easily be resolved over the Internet in this manner, and the plastics manufacturers avoid a cost-intensive and time-consuming servicing on-site. This results in higher machine availability and greater productivity in manufacturing.
Status reports in real-time
An analyzing tool provides status reports and measurement results. The machine operator can even carry out software updates quickly and safely using the online data link. The remote functions can also be used in-house at the customer, for example by the on-duty service staff or for maintenance work. To later retrace modifications and updates, all service activities and their results – such as maintenance, repairs, software updates, measurements and notes – are stored in a logfile.
In addition, the system includes documentation management for storing manuals and internal instructions. This makes all documents readily available at all times and can be kept up to date on demand through updates. ENGEL e-service.24 thus provides a quick fix on failure as well as transparency for the operating and service staff on-site at the injection molding plant.
Source : http://www.engelglobal.com/